Making Safety Seen on International Women in Engineering Day
by Victoria Kushner and Bill Neuburger on Jun 22, 2023 10:30:00 AM
What is International Women in Engineering Day?
International Women in Engineering Day (IWED) occurs annually on June 23rd. It was initiated by the Women’s Engineering Society (WES) in the United Kingdom and has grown to an international celebration reaching millions worldwide. The goal of the celebration is to bring recognition to women’s contributions to engineering, a profession in which women have been historically underrepresented.
Each year, IWED selects a different theme to spotlight. This year’s theme is “Make Safety Seen”. The goal is to profile innovative women who contribute to making people’s lives safer, healthier, and better overall. Previous themes include “Imagine the Future” and “Innovators and Inventors”.
Why is it Important?
Everyone’s heard the stories of the hardships women have endured to get their voices heard. Initiatives like IWED provide a stage for women to be seen, recognized, and celebrated.
In the US, women represent 16.1% of engineers and architects1. That number diminishes even further when we look at Mechanical and Electrical engineers, most degrees held by Hallam-ICS’s workforce, where women make up 9% and 10% of the engineers, respectively1. Imagine walking into a room of similar-looking people. And those people look opposite to you. This is the daily existence for someone in the 9% or 10%. Imposter syndrome, tokenism, and bias abounds.
Despite being 2023, women everyday still experience different treatment. Since joining the engineering community in 2018 I have experienced:
- “What’s your role here, young lady?”
- Ill-fitting or unavailable safety equipment.
- A client wishing to form a nonprofessional relationship.
- Being talked over.
- Overhearing contractors complain about how they hate working for women and do everything to anger their manager, so she quits.
- Assumptions I don’t want to get dirty or break a nail.
- Jokes about clients wanting to “off” their wife.
These are just a few of my experiences, and I am not isolated. Days like IWED bring recognition to organizations like WES and Society of Women Engineers (SWE) that provide a network of support and resources, made up of people who share common experiences. It has personally brought me comfort that I am not alone. And these organizations have equipped me with appropriate responses and increased my confidence in these uncomfortable situations.
Hallam-ICS Employees #MakeSafetySeen as Professional Engineers and Consultants
The term “Professional Engineer” does not mean someone who is dressed smartly and is polite. Professional Engineers are licensed by the states to perform engineering design work in the built environment. Professional Engineers take a creed as part of licensure:
Source: National Society of Professional Engineers
As the creed describes, the role of a Professional Engineer is service to the public. We design systems the public utilizes, and we understand the risk our systems pose. Their lives are in our hands and our foremost responsibility is to protect people. Safety and service is the core of our profession.
This responsibility is an 8-year process to qualify for licensure:
- Bachelor’s degree (four years) at an ABET-accredited college or university.
- Take and pass the Fundamentals of Engineering (FE) exam (a 6-hour written exam).
- Serve as an Engineer in Training (EIT) or Engineer Intern (EI) – state dependent nomenclature – for four years under a licensed Professional Engineer. An easy way to meet this requirement is to work at a engineering firm like Hallam-ICS.
- Take and pass the Principals and Practice of Engineering (PE) exam (a 8-hour written exam).
Hallam-ICS takes pride in our culture of safety – physical safety so everyone gets home, plus emotional safety to empower employees to speak up about harassment or unsafe work environments, advocate for personal growth, and create mentorship relationships with colleagues. A story of our commitment to safety, probably apocryphal, tells of a time someone brought an expired hard hat to work once and her manager noticed and forced her throw it away in a New York City garbage can. It definitely wasn’t me.
Safety Story by Bill Neuburger
We unfortunately learn some safety lessons when things go wrong; they tend to be memorable.
In the 1990s consulting engineers were not savvy to arc flash risk or safe work practices around live electrical equipment. I was working as an energy engineer in Long Island, NY and we were working on a project in an elementary school there. Our scope included some short duration power metering of the existing electrical panels. Like many schools in Long Island, this school was built circa mid 1950s with a three phase, 208-volt system. The electrical distribution included a utility vault with low voltage circuit breaker, supplying a main fused switch in the electric room.. The switch fed two 400-amp distribution circuit breaker panels. Those panels fed smaller panels throughout the school.
We were visiting this project during the summer, only staff were present. My work included removing the covers from the 400-amp panels and installing the short term metering equipment. The covers on these panels were, by today’s standards, massive. They were physically large and quite heavy. Working alone (mistake 1) I leaned against the panel and loosened the fasteners holding the cover to the panel. Then I attempted to slide the cover down to the floor (mistake 2). The cover’s design included features that bent into the panel, forming a frame around the recessed circuit breaker faces. I did not observe the cover’s geometry (mistake 3). As the panel slid, cover’s inwardly bending pieces contacted the bus bar that ran uninsulated through bottom trough area of the panel (not at all a current practice, but the 1950s was a heck of a decade).
When that bit of carbon steel sheet metal contacted the bus bar, it faulted that phase directly to ground. Hot sparks flew out of the panel in all directions. Some of those sparks bounced off the ceiling and landed on my head (no hardhat, mistake 4). Add the sound of the forming plasma and the smell of burning metal and I was a surprised engineer (putting it mildly).
Fortunately for me, the only obvious effect was the cover was welded to the bus bar. The aftermath included the utility breaker clearing and the fuse in the main fused disconnect melting. Thankfully my colleague was older, calmer, and wiser than me. After confirming I was uninjured, he told me the most important thing is my health, and there seemed to be no building damage (right move 1). We opened the fused disconnect and figured out which fuse was blown and went to a local electrical supply house for a replacement (right move 2). We installed the good fuse, closed the switch and discovered the there was still no power on the phase which I shorted with the cover.
We called the utility who dispatched a line worker right away. He entered the pit and using the customary insulated pole/hook, reset the utility breaker (right move 3). Power restored; we completed our work. That day was a long one for me, with a constant fear of repercussions. My colleague reassured me we were OK a second time and we called our client, the facilities director (right move 4). The director was nonplussed and grateful we called.
I share this story to illustrate a few things.
- A combination of factors prevented injury or physical damage. Proper electrical bonding and grounding ensured the fault would clear quickly. The panel cover’s position at the time of the fault was fortunate, protecting me from plasma and sparks. Having personal protective equipment would have protected me better. Alternately, in my non-protective clothing I would have been burned if the cover did not block the plasma and sparks.
- Working on unfamiliar live electrical equipment alone with no safety equipment is a terrible idea.
- Simply jumping into a project without some planning is also a terrible idea. Some of our clients require a job hazard assessment for many tasks, which can seem burdensome. Those assessments have a purpose, though we do not always understand it until it is too late. One favorite client of mine has a Take 5 policy. For five seconds before you do something, look around, think through what you are planning to do, then take deliberate action. If I had done a job hazard assessment or taken 5, I would have observed the panel’s unique geometry and taken a moment to look how the electrical distribution routed. In 5 seconds, I could have identified sliding the panel down was not a safe plan.
- We are all human and prone to error. Most of the time our errors are minor and easy to remedy. Sometimes they are significant (needing to pry a cover panel off a bus bar or buy an 800-amp fuse). Other times they are deadly. As an industry, over time, we have developed systems to protect ourselves and each other. These systems include simple activities like Take 5 and complicated, labor-intensive ones like a peer review of design documents.
Sometimes we take safety for granted, I was lucky enough to learn how effective those safety systems are, even when I undertook a foolish activity.
“Employment.” Society of Women Engineers, 30 May 2023, swe.org/research/2023/employment/#:~:text=The%20percentage%20of%20female%20engineers,information%20research%20scientists%20are%20women.
About the Author
Victoria Kushner - Tori is part of the engineering team in the Vermont office and has been with Hallam since 2017. She designs mechanical, plumbing, and process systems on a variety of projects ranging from cleanrooms & higher education labs to paper mills & farms.
William Neuburger -
Bill has been a mechanical engineer since 1995 and with Hallam-ICS since 2010. His career has brought him to the top of the Transamerica Pyramid Center, chemical plants, underground mines, paper mills, and semiconductor fabrication facilities. He has experience designing, specifying and installing mechanical and electrical systems in the built environment covering industrial, institutional and commercial facilities.
Read Victoria's Hallam Story Bill's Hallam Story
About Hallam-ICS
Hallam-ICS is an engineering and automation company that designs MEP systems for facilities and plants, engineers control and automation solutions, and ensures safety and regulatory compliance through arc flash studies, commissioning, and validation. Our offices are located in Massachusetts, Connecticut, New York, Vermont, North Carolina, Texas and Florida and our projects take us world-wide.
You May Also Like
These Related Stories
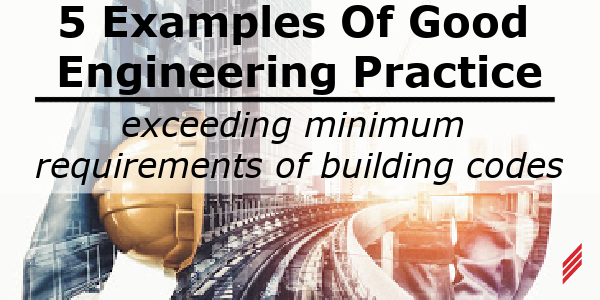
5 Examples of Good Engineering Practice Exceeding Minimum Requirements of Building Codes
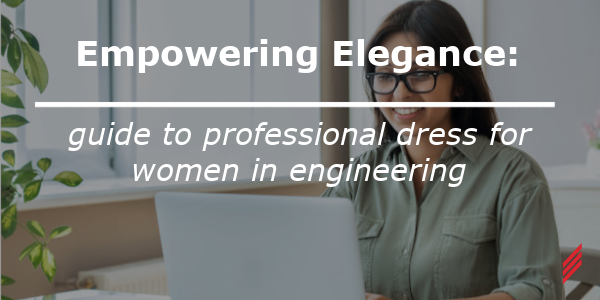
Empowering Elegance: Guide to Professional Dress for Women in Engineering
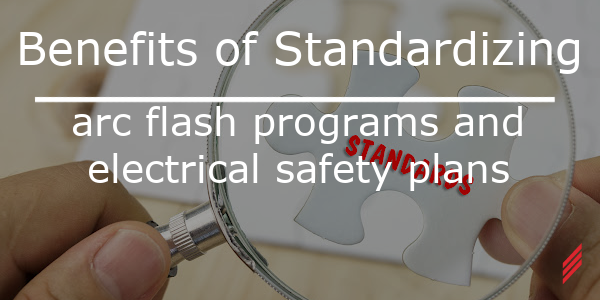
No Comments Yet
Let us know what you think