Programming with Rockwell Automation's PlantPAx
by Thomas Toppin on Sep 30, 2021 11:30:00 AM
For those of you that are new to PlantPAx I’d like to give a brief overview of the system and explain some of the features that truly make it a modern day DCS. PlantPAx is a plant wide control system that utilizes a common automation platform to seamlessly integrate both process and discrete control as well as plant wide information.
Another blog you might find useful:
Programming with PlantPAx - Program Structure & Controller Configuration
The system is designed to be scale-able and modular, utilizing a range of different architectures depending on your needs. Unlike most DCS systems PlantPAx uses open communication standards by utilizing Ethernet/IP. This allows for the use of other off-the-shelf products to easily integrate into the system and the ability to share real-time data right up to the enterprise level.
In order to be a true PlantPax system there are certain design criteria that must be followed to guarantee performance. Rockwell provides a PlantPAx selection guide that assists with selecting the system architecture and components.
Even though this blog series will be focusing on actual programming methods I think it’s important to understand the key elements that make up a PlantPAx system. The following is a list of system elements and a diagram of a typical system architecture that will help with getting familiar with the system.
Software
- Studio 5000 Logix Designer® application
- Studio 5000 Architect™ application
- FactoryTalk® View software
- FactoryTalk Batch software
- FactoryTalk AssetCentre software
- FactoryTalk VantagePoint software
- FactoryTalk Historian software
Process Automation System Server (PASS)
- The PASS server is an essential element that hosts the data server, alarm server and HMI server
Engineering Workstation (EWS)
- The EWS is where all system configuration, application development, and maintenance is done.
Operator Workstation (OWS)
- The OWS is where operators interact with the PCS and is not intended for maintenance and development.
Operator Workstation Application Server (AppServ-OWS)
- Uses Remote Desktop Services (RDS) to serve up data to multiple thin clients
Historian (AppServ – Info)
- Contains historian application to collect, manage, and analyze data.
VantagePoint (AppServ-Info)
- Contains VantagePoint application
SQL Server (AppServ-Info)
- The SQL server is used by FactoryTalk Batch, AssetCentre, and VantagePoint to store and access process data as well as FactoryTalk Alarm and Event (FTAE)
Asset Management Server (AppServ-Asset)
- Adds maintenance and plant operations to assist with diagnostics, real-time monitoring, and calibration.
Batch Management Server (AppServ-Batch)
- Manages recipes, materials, and procedural control.
Domain Controller
- Used by PlantPAx to store user account data, authenticate users, and handle security policies.
Process Controller
- PLC
Now that I’ve bored you to death I’d like to talk about one of the key advantages of a PlantPAx system, the library of process objects. The library contains predefined code (Add-On Instructions), display elements (global objects), and face plates that have all been tested for functionality and performance. These objects provide consistency for both the operators and the engineers and once mastered give them the ability to make control of their system easy and effective. I recently had the opportunity to integrate a PlantPAx system for a client of ours and I was truly impressed with the development and engineering capabilities. In the following series I’d like to briefly get into some of the methods and best practices that we used as well as some of the tools that are provided to expedite both the HMI and PLC development process.
- What is the library of process objects?
- Program Structure & Controller Configuration
- The benefits of user defined data structures
- Adding an Add On Instruction (AOI)
- Creating display objects
- The Importance of naming conventions
- OPC configuration tool
- Alarm handling with PlantPax
- Simulating with PlantPax
- The Importance of naming conventions
What is the library of process objects?
In order to follow some of the topics I’ll be discussing it’s very important to understand the library of process objects. Basically the library is suite of predefined controller code or add-on instructions (AOI), display elements and face plates that is provided and supported by Rockwell. Each add-on instruction is developed for a particular use ranging from digital inputs to PID controllers and Powerflex drives. Inside each AOI is premade logic that has been developed and tested by Rockwell for a specific application. Each add-on instruction has a matching graphic display (face plate) which communicates directly with each instance of the add-on instruction. Each face plate is designed to configure, maintain, and operate the AOI which gives the operators the ability to make changes to the PCS without digging into the PLC logic. Everything from scaling, engineering units, P&ID tag names, delay SP, alarm names, alarm SP and alarm severity can be configured right from the face plates.
Every AOI and corresponding face plate have different capabilities depending on it’s application. For instance an analog input (P_AIn) AOI will have different features compared to a discrete output (P_DOut).
Even though there are differences with each object it is important to understand the similarities between all of them. Every object is created in FBD format and contains input and output parameters that can be connected/mapped easily. Every AOI uses the same naming conventions to help understand the purpose of the tag. For instance all inputs to the AOI begin with Inp_ and all configuration tags begin with Cfg_ . When applicable, the same exact naming convention is used from one instruction to another which keeps things consistent.
Every face plate has the same layout and graphic icons that allow the user to easily navigate each object. At the top of every face plate are a set of tabs that open up different screens pertaining to that particular instance of the object. Most face plates have the following tabs at a minimum. There are cases where the face plate has more tabs that are only needed for that type of object. Below is also an example of screen layout for a P_Din (Discrete Input) AOI.
As you can see there are multiple configuration settings that can be changed with the click of a mouse which gives the user the ability to make changes that would typically be needed to be done using PLC software and by a control’s engineer. The face plates also contain built in security which assures that certain users can only make certain changes to the system is easily achieved.
To find out more about Rockwell’s Library of process objects you can follow the link below.
http://literature.rockwellautomation.com/idc/groups/literature/documents/rm/proces-rm002_-en-p.pdf
About the Author
Tom Toppin is a Process Controls Engineer for Hallam-ICS. Tom started his career as an Electrician and has over 17 years’ experience designing, installing & troubleshooting electrical systems. Since becoming a Controls Engineer Tom has developed and commissioned a range of systems and his areas of expertise include continuous processing, batch processing, SCADA, water and wastewater.
Read My Hallam Story
About Hallam-ICS
Hallam-ICS is an engineering and automation company that designs MEP systems for facilities and plants, engineers control and automation solutions, and ensures safety and regulatory compliance through arc flash studies, commissioning, and validation. Our offices are located in Massachusetts, Connecticut, New York, Vermont and North Carolina and our projects take us world-wide.
You May Also Like
These Related Stories
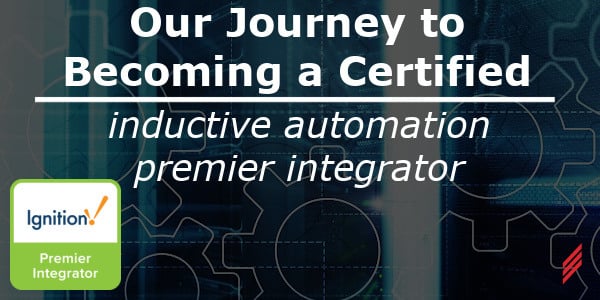
Our Journey to Becoming a Certified Inductive Automation Premier Integrator
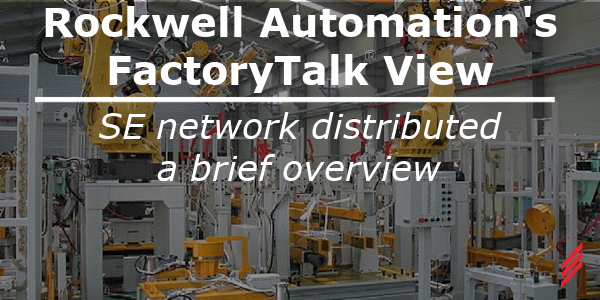
Rockwell Automation’s FactoryTalk View SE Network Distributed – A Brief Overview
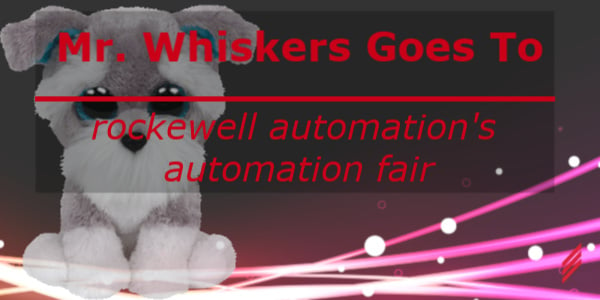
Comments (6)