Replacing Your Obsolete Control System. Step 2 – Upgrade the PLC Hardware
by Julie Gruenholz on Apr 16, 2020 10:23:00 AM
Upgrading your obsolete control system is a helpful 7-part blog series addressing the important technical aspects of upgrades and written by an industry professional with over 25 years of experience.
Here are links to the other blogs in this series:
6 Questions to Ask When Upgrading an Obsolete Control System While Keeping Your Plant RunningKISS and 5 Other Items to Consider when Choosing to Upgrade Your PLC Platform
Replacing Your Obsolete Control System. Step 1 – Replace the SCADA
Replacing Your Obsolete Control System. Step 2 – Upgrade the PLC Hardware
Replacing Your Obsolete Control System. Step 3 – Key Considerations when choosing the new SCADA/HMI.
A note for Mechanical Engineers… Don’t be afraid of the PLC programmer or the control system software. (future blog)
How can you run your plant with a mix of old and new hardware at the same time? – An editorial on S88.
Hopefully in my last article called “How can your operators effectively run your plant during an automation system conversion with a mix of old and new hardware and software?”, I convinced you to upgrade your SCADA front end before you start to upgrade your PLC hardware. The most effective way forward is to have a stable front end that everyone is comfortable with. Then, behind the scenes you can start to convert your control system, small piece, by small piece, from your obsolete control system hardware to new PLC controls.
Converting the Control System Hardware
After you have an upgraded, proven, front end you can start to convert your control hardware. Each new PLC should control a small portion of your plant. The trick is to break your plant into small enough chunks that converting one section at a time will not take down your plant’s production capabilities. Take the time to consider the entire control system architecture and how your equipment is grouped. The smaller you can make each control group, the easier it is to convert one group at a time. Separate your small control chunks into separate PLCs and plan to pass information across your network. Temporarily, you can use your front end to pass information from old controllers to new PLCs. When you are finished, you want the PLCs to be able to have complete control, and pass information among themselves, without relying on the front end. But during the conversion, passing information via the front end might allow you to break the system into more manageable sections.
In the long term, you don’t want to pass information that needs instantaneous updates across the control system network, such as having a controlling sensor (process variable) in one PLC and the controlled device (control variable) in another PLC for a critical, fast moving, PID loop. Of course if you have many controlled devices that all follow the same PID output (like many pumps that all run at the same speed), it might suit your needs to have the pumps in many PLCs where you can count on the network latency not to affect process responsiveness. There are many other types of information that can be passed where network latency is not an issue. Perhaps you have several pumps, which can all back each other up, that need to be started and stopped by a single automatic process trigger. All these pumps do not need to be in the same PLC. The automatic process trigger can reside in one PLC and send the start and stop commands over the network.
Utilizing S88 for Standardization and Simplicity
The key with any conversion is standardization and consistency. There is a standard design philosophy that describes how to cut your control system into small consistent chunks called ANSI/ISA-88 (S88 for short). This is a standard that has been designed for Batch Processes, but should be applied to every control system and all software. The spirit of the standard should be stolen and applied to continuous processes.
No control system is overwhelming if you break it down into its smallest components. When writing the PLC software, look at your entire control system and see where there is similar equipment and apply the spirit of the S88 standard. For instance, perhaps you have several pumps. These pumps may be used to move different liquids for different processes, but in your new control system make these all function the same. Perhaps in your plant, each pump is on a VFD and each pump needs these components:
- Start/Stop control
- Speed control
- Run Status monitored
- Auto and Manual Status monitored
- kW monitored
- Runtime calculated
Make a function block in your new code that handles all these things. As you are converting equipment to new PLCs, you can program each pump with this new, tested, function block and the checkout time for each element will be greatly decreased. This function block should also correspond to a consistent control and display setup on your front end.
Read the next blog in this series
There is a good chance that we have already helped a customer with your exact problem. For advice on upgrading your obsolete control system you can contact us via
About the Author
Julie has left Hallam-ICS to pursue other endeavors, but her contributions to the company continue to be valued.
About Hallam-ICS
Hallam-ICS is an engineering and automation company that designs MEP systems for facilities and plants, engineers control and automation solutions, and ensures safety and regulatory compliance through arc flash studies, commissioning, and validation. Our offices are located in Massachusetts, Connecticut, New York, Vermont and North Carolina and our projects take us world-wide.
You May Also Like
These Related Stories
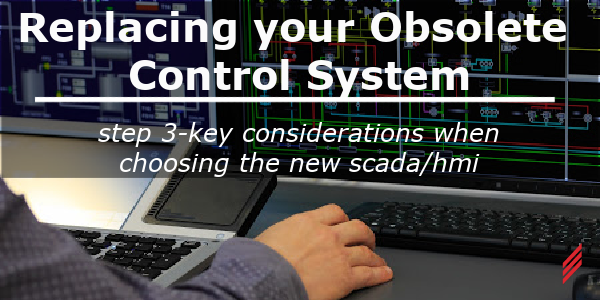
Replacing Your Obsolete Control System. Step 3 – Key Considerations when Choosing the New SCADA/HMI
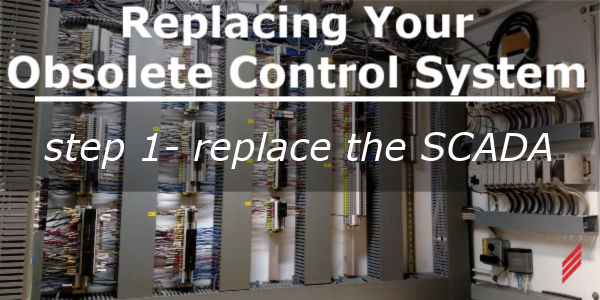
Replacing Your Obsolete Control System. Step 1 – Replace the SCADA
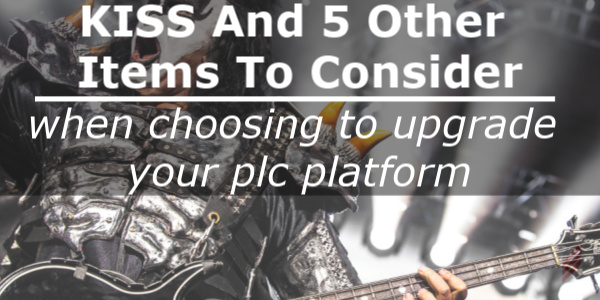
Comments (1)