KISS and 5 Other Items to Consider when Choosing to Upgrade Your PLC Platform
by Julie Gruenholz on Apr 9, 2019 10:32:00 AM
Upgrading your obsolete control system is a helpful 7-part blog series addressing the important technical aspects of upgrades and written by an industry professional with over 25 years of experience.
Here are links to the other blogs in this series:
6 Questions to Ask When Upgrading an Obsolete Control System While Keeping Your Plant RunningKISS and 5 Other Items to Consider when Choosing to Upgrade Your PLC Platform
Replacing Your Obsolete Control System. Step 1 – Replace the SCADA
Replacing Your Obsolete Control System. Step 2 – Upgrade the PLC Hardware
Replacing Your Obsolete Control System. Step 3 – Key Considerations when choosing the new SCADA/HMI.
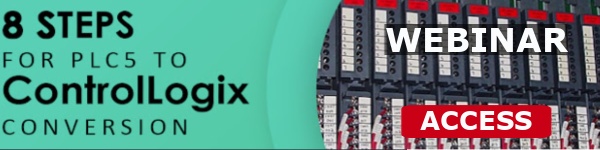
What PLC hardware will the new automation system use?
So, you are either being forced to, you are excited to, or you see it as your personal quest to upgrade your obsolete control system. No matter your motivation, you need to decide what building blocks you will use to make your new control system exquisite. The basic building block that will run each section of the plant is the PLC. Which PLC hardware should you use? Every manufacturer will try to sell you on the plusses of their system. Keep in mind:
- KISS: I’m a fan of the rock group, but also a fan of “Keep It Simple, Stupid”.
- Everything you encounter as you go through the design process will make your automation system more complicated. Make sure your basic design philosophy is as simple as possible.
- Frequently, simplicity means matching a site standard. You may not agree that a site standard is the best way forward, but installing a PLC platform for which you already stock spare parts and already have in-house troubleshooting knowledge will be a big advantage in the future.
- Take the long view:
- Your current automation system hardware has been installed for 20 or 30 years. The new hardware will probably be there just as long.
- Specific features that you, or others in your plant are comfortable with now, may be leading you to installing a certain hardware platform. These features will be irrelevant in 10 years.
- All PLC platforms offer almost the same features:
- From Rockwell to AutomationDirect, you can make any platform work in your plant.
- Engineers at a company manufacturing PLC hardware that is lacking certain features are feverishly making improvements so their product has all the features available in the competitor's product.
- Assuming your project will evolve over several years, the features available for every PLC platform will change.
- Even if a certain PLC platform is lacking a feature that you find attractive, the same feature can probably be achieved with a couple extra steps in any other platform.
- Network Integration and Communication:
- One of the biggest costs of control system installation is network cabling. If you are in a cost crunch, this may be something that significantly affects your PLC choice.
- Although it may not be that significant to keep your plant running, you should put some emphasis on upgrading your automation system communication. Whether your legacy system has the capability or not, the folks providing money to upgrade your control system expect to see real time data and colorful graphs on their desktop.
- If you decide to provide control system information to your manager’s desk, you need to consider the security issues associated with communicating between your control system (OT – operational technology) network and the corporate IT Network. An OT network has different design and maintenance requirements than an IT network.
- Most plants and most modern PLC platforms are communicating over Ethernet. While it would be great to be able to hook all of your new PLCs together over a new Ethernet network, this may be way too expensive. I suggest using old network wire now and have a plan to convert to Ethernet in the future. If you plan now, it might be possible to change the network hardware with almost no future software changes.
- Think inside somebody else’s box:
- It might make more sense to figure out how to make the hardware you already have in your crib work for an upgrade, than trying to figure out how to get your ideal PLC to work with the infrastructure that you have.
- There will always be hoops to jump through to move from one hardware platform to another. Think of complicated connections (like an HMS Anybus Gateway) as a temporary solution to get you over an implementation hump. But, have a plan to eliminate complicated bottlenecks in the future.
- Consider system architecture:
- Do you want centralized or distributed control?
- There are many valid arguments for both if you have a Greenfield project. But, when upgrading an obsolete control system, during the entire conversion (this may be several years), there will be little pieces of your plant controlled by old and new controllers. These controllers do a specific task and need to be autonomous. This means distributed control is probably the best answer.
- If your new control system is going to have distributed control, consider how to break your plant down into small chunks, with a separate PLC controlling each chunk. These PLCs all need to communicate together and communicate to a SCADA or HMI.For advice on upgrading your specific hardware situation, contact us below. There is a good chance that we have already helped a customer with your exact problem figure out how to upgrade their obsolete automation hardware.
Read the next blog in this series
For more information please contact Julie directly at jgruenholz@hallam-ics.com or visit our
About the author
Julie has left Hallam-ICS to pursue other endeavors, but her contributions to the company continue to be valued.
About Hallam-ICS
Hallam-ICS is an engineering and automation company that designs MEP systems for facilities and plants, engineers control and automation solutions, and ensures safety and regulatory compliance through arc flash studies, commissioning, and validation. Our offices are located in Massachusetts, Connecticut, New York, Vermont and North Carolina and our projects take us world-wide.
You May Also Like
These Related Stories
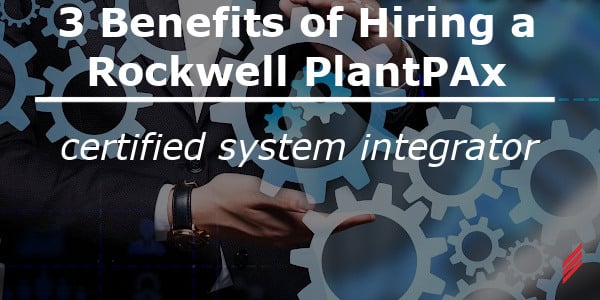
3 Benefits to Hiring a Rockwell PlantPAx Certified System Integrator
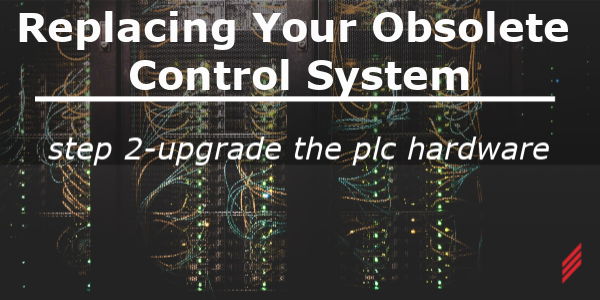
Replacing Your Obsolete Control System. Step 2 – Upgrade the PLC Hardware
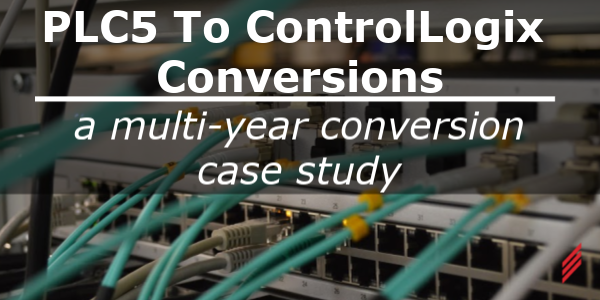
No Comments Yet
Let us know what you think