Replacing Your Obsolete Control System. Step 3 – Key Considerations when Choosing the New SCADA/HMI
by Julie Gruenholz on Sep 3, 2020 10:30:00 AM
Upgrading your obsolete control system is a helpful 7-part blog series addressing the important technical aspects of upgrades and written by an industry professional with over 25 years of experience.
Here are links to the other blogs in this series:
6 Questions to Ask When Upgrading an Obsolete Control System While Keeping Your Plant RunningKISS and 5 Other Items to Consider when Choosing to Upgrade Your PLC Platform
Replacing Your Obsolete Control System. Step 1 – Replace the SCADA
Replacing Your Obsolete Control System. Step 2 – Upgrade the PLC Hardware
Replacing Your Obsolete Control System. Step 3 – Key Considerations when choosing the new SCADA/HMI.
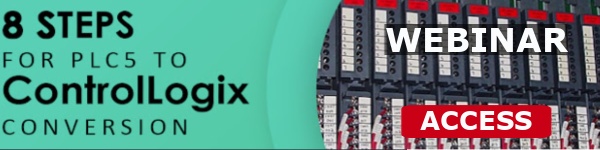
What SCADA or HMI will the new automation system use?
Don’t you wish you could just imagine how you want your equipment to operate and it would obey? Yea, we’re not there yet… You need to provide a way for the humans in your plant to communicate with your equipment.
When you are migrating from an obsolete control system to a new control system in your plant, you need to keep your plant functioning. It is critically important to have a stable front end (SCADA or HMI) that everyone is comfortable with. Your operators will need to not only run the plant like they have in the past, but they will need to have the ability to take manual control and perhaps use some existing features that are seldom used along with controlling the new equipment. It is critical that while you are thinking of how to make everything (old and new) work together that you give your team the best tools that you can. Consider these topics:
User Friendly Layout
You need your operators to be comfortable with the HMI/SCADA and have all the tools they need to manipulate the old and new equipment. The existing front end may look completely indecipherable to you, but it may be easy for your operators to navigate. Many existing control systems have evolved over years. For various reasons they may be laid out in a way that was convenient for the system on which they were originally developed, but may make little sense to you and may not be a reasonable or convenient way to build a new front end.
It is important to strike a balance between the existing and new front ends. If the layout of the new front end is too different from the old, operators may not be able to react quickly and may get discouraged with too many changes. Most humans do not like to learn a new system, especially if it is for equipment that has been working just fine for years. If the layout of the new front end is too similar to the old, you may be copying features that are cumbersome to implement on the new system. It is best to keep your new front end as simple as possible and use the features it contains in the way that the manufacturer intended. If you have to customize controls too much to make your screens look like the old system, you may be building a lot of overhead into a system that is unnecessary and difficult to maintain. It is a fine line that you need to walk to make your operators happy, by not changing too much, and make your new front end as simple and practical as possible.
Connectivity
Ideally you want your new front end to talk to both the old and new control system. Most modern front ends can talk on any network protocol. If your new front end doesn’t come standard with a driver for your old control system, consider hiring someone to write a driver to use during conversion so the screens that control old and new systems can be moved between seamlessly. Your operators should not have to know if they are controlling equipment connected to either an old or new control system. They should both work the same.
If you are using local HMIs, make sure you have a separate HMI for each chunk of equipment that is upgraded. You might need more HMIs than you would if you were building your plant from scratch. If a whole piece of equipment is upgraded and on a new HMI, make sure the old equipment controls are easily accessible.
If you are upgrading from a push-button/selector switch/pilot light system to an HMI, buy more HMIs than you think you need. Avoid making people walk long distances to turn equipment on and off or get critical data. This will alleviate stress and make your project a success.
Architecture
The best front end is:
- Accessible
- Easily maintained
- Robust
For easiest maintenance, all front end screen changes would be made in one place. You can install a system like this with a single SCADA system that controls everything, leveraging thin clients or portable tablets for local control. But, this can allow for a single point of failure and can leave critical equipment uncontrollable.
You can use multiple, distributed SCADA systems, all with common screens. You still have a single point of failure on your thin client server, but perhaps this is an unnecessary feature during a server failure. This creates more cost and maintenance as several servers will need to be maintained, but if one SCADA fails you don’t lose control of your whole plant.
You can use HMIs for more distributed control. This makes migration easy. As you update each piece of equipment, you can add a dedicated HMI. Connectivity between old and new control systems is not an issue. There will be several HMIs that need to be maintained, but if all are the same model, a hardware spare can quickly be brought on line by downloading the appropriate configuration. Of course with just simple HMIs, you have limited ability to produce trending and reporting.
Some plants use a mix of SCADA and HMIs. This allows for the benefits of both a SCADA system and the distributed control of an HMI. Unfortunately, having to pay someone to program both a SCADA and a local HMI is costly and changes are not necessarily made identically on both devices.
As I’ve said in previous blog, it is best to convert the front end first. Make sure the operators are proficient using it before changing the control system hardware. During the upgrade to a new control system, you need the operators to be able to operate both the new and existing equipment and be able to run things in a less than ideal situation. Don’t make things any more difficult on your operators than you have to. You all have to work together during a control system conversion. It can be frustrating for everyone and operators who are comfortable and proficient can save your ass when something goes awry.
Read the next blog in this series
No control system is overwhelming if you break it down into its smallest There is a good chance that we have already helped a customer with your exact problem. For advice on upgrading your obsolete control system you can contact us via
About the Author
Julie has left Hallam-ICS to pursue other endeavors, but her contributions to the company continue to be valued.
About Hallam-ICS
Hallam-ICS is an engineering and automation company that designs MEP systems for facilities and plants, engineers control and automation solutions, and ensures safety and regulatory compliance through arc flash studies, commissioning, and validation. Our offices are located in Massachusetts, Connecticut, New York, Vermont and North Carolina and our projects take us world-wide.
You May Also Like
These Related Stories
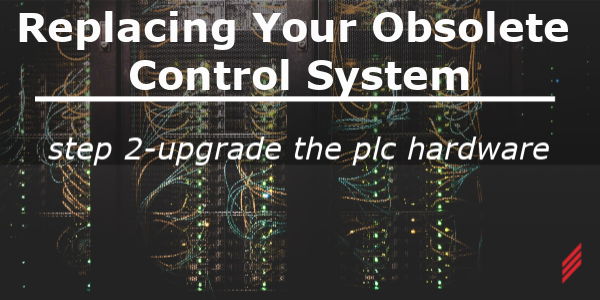
Replacing Your Obsolete Control System. Step 2 – Upgrade the PLC Hardware
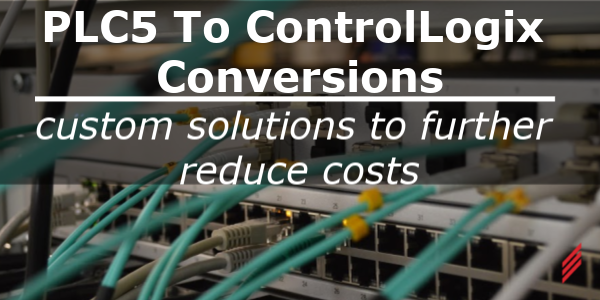
PLC5 to ControlLogix Conversions – Custom Solutions to Further Reduce Costs
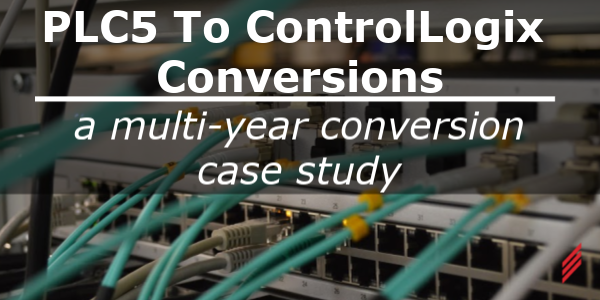
No Comments Yet
Let us know what you think