Rockwell Automation’s PlantPAx 5.0 – Understanding the Changes
by Sam Lacasse on Jun 16, 2022 10:30:00 AM
Take the time to get acquainted with the newest changes to PlantPAx version 5.0
WHAT
If you are new to PlantPAx, welcome! PlantPAx in concept is the result of Rockwell Automation’s development of standardized FactoryTalk View Studio HMI Faceplates with Studio5000 Add-On Instructions (AOI). Here is a link to Rockwell Automation’s PlantPAx modern DCS (Distributed Control System) website if you would like to get more familiar with the system and its components.
In the latest release, Rockwell Automation has made considerable changes to PlantPAX 5.0. Hopefully, this blog can help the reader accelerate the learning curve based on our recent experience. The changes are not trivial. Do yourself a favor and take the time to understand the changes and how it will affect your projects and the budget.
INTRODUCTION
Hallam-ICS has been implementing PlantPAx since version 3.0 for Life Sciences, Food & Beverage, and Industrial clients. It was certainly a leap to come from a traditional state machine programming mentality with lots of colors within the HMI to the new drive toward a high-performance HMI. Rockwell joined the revolution and developed standards to aid developers in reducing development time while delivering standardized functionality, look and feel. Each revision of PlantPAx has addressed user requested improvements, additional functionality, integrated features, and advanced development tools.
SUPPORTED PROCESSORS
One of the major changes in PlantPAx 5.0 is that the AOIs are now embedded in the firmware of the process controllers. Because of this, PlantPAx 5.0 is now supported by specific processors starting with version 33, as identified by Rockwell Automation’s Knowledgebase Document ID QA63192. This article states that ControlLogix 5580 1756-L81EP, 1756-L83EP, 1756-L85EP and CompactLogix 5380 5069-L320ERP, 5069-L340ERP support PlantPAx 5.0. These processors end in “P” identifying Process controllers. This ensures the AOI revision and functionality will be preserved because it does not allow changes to the AOI or the ability to ‘look under the hood.’ See the knowledgebase for options supported if the process controller is not an option for your application.
PROGRAMMING CHANGES
In PlantPAx 5.0, you can now fully configure the AOI faceplate within Studio5000. You can navigate to each tab to configure general, scaling, alarming, associated IO status/faults, and so on. RSLinx is no longer a requirement to get online with the controller in versions above v33 because FactoryTalk Linx is used instead and is part of the licensing of Logix Designer for basic communications.
FactoryTalk Alarms and Events are initiated from the Process Automation Controller (PAC). This is not a new concept but has been expanded to be fully integrated into the AOI in PlantPAx 5.0. The AOI allows configuring of alarms from within the PAC through the configuration pop-up screen that has multi-tabs and sub-screens.
FT Historian trending has also been included as part of the AOIs and Faceplates. Configuring the AOI properly will allow the export of all configured points using the advanced configuration tools provided with PlantPAx 5.0. The PlantPAx faceplates can be configured to show historical trends if the functionality is enabled.
Additionally, the newest configuration utilities allow you to set some of the configuration parameters but not all. See my feedback below.
DEVELOPMENT TOOLS
Rockwell Automation’s FactoryTalk Logix Echo is the newest emulator available. We were not able to get a loaner processor in time to test our application, so Echo was the next best thing. We were able to get a loaner license from our local Rockwell Distributor and used it almost immediately. Echo was a huge help in being able to be prepared to respond to some of the changes associated with the latest firmware changes in PlantPAx 5.0. I highly recommend using Echo if you have the opportunity.
HONEST FEEDBACK
To configure an analog point for the first time with PlantPAx 5.0 was a very time-consuming experience. Just imagine configuring an alarm for Hi-Hi including delays, severities, shelving, messages, tags embedded into the message, class, alarm groups, latched, acknowledgement, etc... from a pop-up screen of the AOI from Studio5000. Then having to do it again and again for High, Low and Lo-Lo alarms. Then having to repeat this process for every point in the system.
Example screenshots:
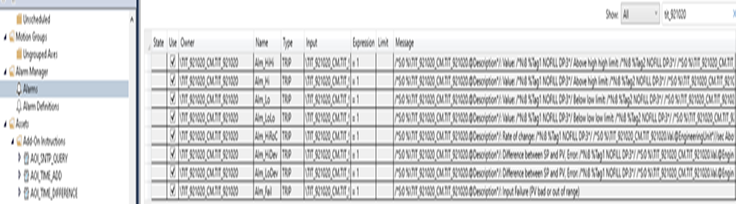
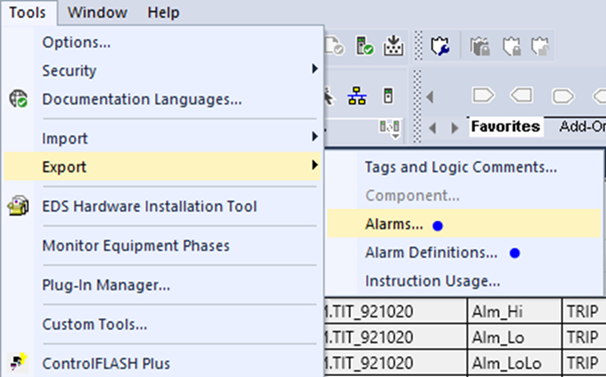
If you are thinking, “What is the big deal? You can configure all of these using the Excel configuration utility,” you would be partially right. One of the major changes Rockwell made in PlantPAx 5.0 was to use the “.@” fields of the Extended Tag properties within the controller. These are currently not accessible externally from Excel/OPC. The current solution in the version we are using is to allow the Excel utility sheet to be created from another utility so you can import your “.@’ changes into the Controller program to update these embedded text fields. We called tech support several times and every technician we spoke with was still learning the product and related updates and took several days to get back to us with suggestions to address our issues.
Rockwell is planning to address this in the next major release, providing the ability to access the “.@” fields using OPC via FactoryTalk Gateway, but this is not currently an option for our latest project.
We belong to a Peer Group of other large system integrators through our involvement with the Control System Integrators Association (CSIA) and took the time to reach out to other members of the Peer Group to have a simple discussion about their experience with PlantPAx 5.0. The intent was to see if we were missing something. We concluded that we did not overlook anything. While there are valuable improvements in the PlantPAx 5.0, the changes made to the latest revision of the development software resulted in added development time for the system integrator. Somewhere to the order 3 to 4 times the time required as compared to previous versions is possible.
It has been a time-consuming process to learn and react to all the changes, but it is like everything else in the automation world. Change is constant!
LESSONS LEARNED and RECOMENDATIONS
- If you do not use the PlantPAx Checklist, I highly recommend you do and everyone on the Automation project team have a hand in completing it. Project managers, IT/OT engineers and programmers need to understand all requirements and changes. We were contracted late in the game on a recent project to implement an application designed by another firm.
- If a design is pre-determined, be sure to request the PlantPAx Checklist and review the entire control system design and functional requirements. If you think something is not part of your scope, be sure you have the details to understand how it can affect the deployment of the system that is in your scope.
- To address replication efficiency issues, be sure to configure each standard AOI block and test it completely before duplicating them. Once the AOI points are created you can export, modify, and import the alarms from the Alarm Manager within Studio5000. The Excel configuration utility is still a useful tool, just be aware of the changes.
- Be sure to accurately quantify all PlantPAx AOI blocks required. Include software points such as Modbus, Ethernet devices, Remote IO (RIO) modules. PlantPAx AOIs can monitor health and fault status of all Rockwell modules. Some projects require this, so be sure this is determined in the initial design phase.
- Education and training are paramount. Send staff to receive and maintain PlantPAx specific Rockwell Automation training.
- Conduct a Factory Acceptance Test (FAT) whenever possible. It reduces risk, reduces time in the field, and ensures design details have been fully resolved prior to installation.
- Careful consideration needs to be taken when merging previous PlantPAx versions with PlantPAx 5.0.
About the author
Sam Lacasse is a Senior Process Controls Engineer for Hallam-ICS with over 20 years of experience. Graduating from New England Institute of Technology 1993 with an A.S. Science Degree. He has extensive experience in Toxic Gas Monitoring, Food & Beverage, Robotics/Vision/Motion control and large scale Water/Wastewater applications.
Read My Hallam Story
About Hallam-ICS
Hallam-ICS is an engineering and automation company that designs MEP systems for facilities and plants, engineers control and automation solutions, and ensures safety and regulatory compliance through arc flash studies, commissioning, and validation. Our offices are located in Massachusetts, Connecticut, New York, Vermont and North Carolina and our projects take us world-wide.
You May Also Like
These Related Stories
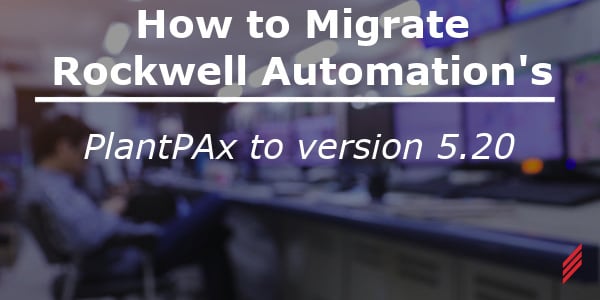
How to Migrate Rockwell Automation’s PlantPAx to Version 5.20
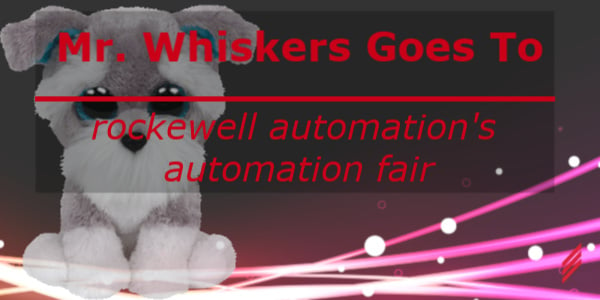
Mr. Whiskers Goes to Rockwell Automation’s Automation Fair
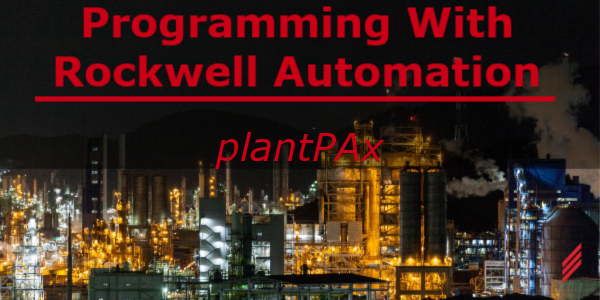
Comments (3)