Turning Your TGMS Safety Requirement Specification (SRS) into an Effective Testing Document
by Dan Maxwell on Aug 27, 2020 10:30:00 AM
A Safety Requirement Specification (SRS) defines the basic functions of a gas monitoring system. The SRS is the root of the design of a Toxic Gas Monitoring System (TGMS). It only makes sense that a completed TGMS installation should be commissioned in reference to this source document. This logic is in alignment with the Good Automated Manufacturing Practice (GAMP) V-model. The details of the V-model are outside the scope of this document, but it is worthwhile to review if you have the interest. Briefly, the V-model matches the specifications produced for a system to the testing performed as part of the verification process.
Logically, a new safety system should be commissioned to assure its proper operation. The open question is; why do I need to commission the system again? If I need to recommission it, how often does it need to be done? The Code does not do a clear job of identifying the answers to these questions. Hallam-ICS has chosen NFPA (National Fire Prevention Association) 72 “National Fire Alarm and Signaling Code” as the basis for our answers to these questions. Although Chapter 14 “Inspection, Testing, and Maintenance” is not specific to Toxic Gas Systems, it gives well thought out directions for a Life Safety System, and is, therefore, a strong model for TGMS.
Converting the SRS into a Site Acceptance Test (SAT) document is a relatively straightforward exercise (although it requires time and patience). It requires a comprehensive understanding of the TGMS inputs and outputs (I/O) from both external devices and internal devices. The SAT intends to provide a script for testing and recording the results of the test. The method I am describing expands the SRS by including all individual input points. The spreadsheet is greatly expanded to provide a place for confirmation initials to be entered by those completing the testing. An example is shown below. The individual gas detection and emergency gas off (EGO) points are shown under their respective categories. From the original SRS, the “X” entries indicate the required actions. Cells not requiring actions are grayed out to make identifying the cells requiring response easier. Initials and dates are entered upon completion of each test.
In the above example, you will notice that the valve manifold box (VMB) and gas cabinet (GC) shutdowns are to be specific to each gas detection point. This information could be kept on a separate document, but the testing process can be complicated enough without shuffling between papers. There are a couple of possible methods to include this information in the SAT. Below is an example of where the required shutdowns are annotated within the initialing cell.
A second option is to expand the output columns to include individual columns for each VMB and GC. This can make the SAT document quite wide. An example is shown below. This method can be useful in cases where multiple VMBs or GCs are required to be shut down by a single gas detection point. Gas Detection in a tool gas box would be an example of this. A tool gas box could have multiple flammable gases entering it from separate VMB sticks or GCs. A flammable gas alarm would likely require the shutdown of all flammable upstream gas sources.
It is also important to include testing for I/O that is internal to the TGMS control system. Examples include: Hard or soft reset buttons for PLC and/or Safety Relays, Horn Silence buttons, and inhibit key switches.
By utilizing the SRS as the heart of your SAT document, you can be sure you are fully capturing the functionality originally intended for your Toxic Gas Monitoring System.
Going back to the beginning of this discussion, there were two questions included, 1) why do I need to retest my TGMS?, and 2) how often do I need to do it? If you subscribe to the idea that a TGMS is a safety system just like a Fire Alarm System, then Using NFPA as our guide, (NFPA 72 – Table 14.4.3.2):
All TGMS components should undergo an annual functional test.
A TGMS is a dormant system. Though a TGMS system is typically wired fail-safe, an annual check of the I/O devices and their connections to the PLC/SCADA is recommended. Much of the connectivity testing involved can be undertaken with simple notification to the users and without disruption of the TGMS and building operations. This would involve testing outputs like the GAN functions and inputs like the FAS (Fire Alarm System) and BMS (Building Management System).
An annual functional test is just one of the service and maintenance items to consider for your TGMS. Please consider reviewing NFPA 72 to see the range of topics you should have in place to keep your TGMS in top shape.
About the Author
Dan Maxwell is a Senior Project Manager with Hallam-ICS’s Toxic Gas Monitoring team. Dan trained in Mechanical Engineering and has worked in Project Management in the construction and manufacturing sectors before coming to Hallam-ICS in 1999.
Read My Hallam Story
About Hallam-ICS
Hallam-ICS is an engineering and automation company that designs MEP systems for facilities and plants, engineers control and automation solutions, and ensures safety and regulatory compliance through arc flash studies, commissioning, and validation. Our offices are located in Massachusetts, Connecticut, New York, Vermont and North Carolina and our projects take us world-wide.
You May Also Like
These Related Stories
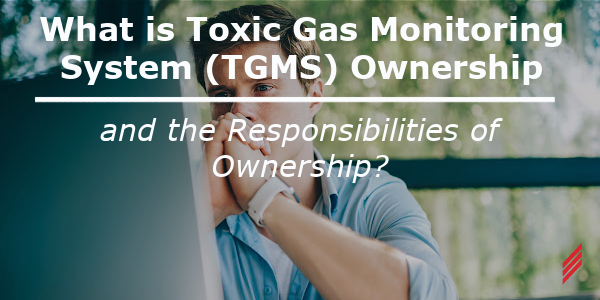
What is Toxic Gas Monitoring System (TGMS) Ownership and the Responsibilities of Ownership?
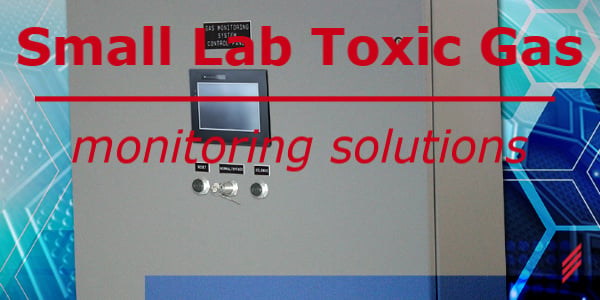
Small Lab Toxic Gas Monitoring Solution
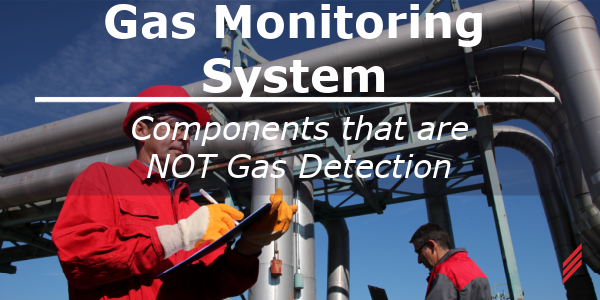
No Comments Yet
Let us know what you think