Why Choose Ignition SCADA from Inductive Automation?
by Jason Barry and Dalton Sheehan on Jul 22, 2021 10:30:00 AM
Overview
Inductive Automation is one of the fastest growing industrial automation software developers primarily because of their Ignition SCADA. In this blog, we will discuss some of the capabilities and advantages of the Ignition platform and what it offers system integrators and end-users.
Ignition Is Different
Ignition competes with several existing SCADA software, including:
- Rockwell FactoryTalk View
- GE iFix
- GE Cimplicity
- Siemens WinCC
- Wonderware Intouch (Aveva)
Like those other SCADA software, Ignition allows you to:
- Control industrial processes locally or at remote locations
- Monitor, gather, and process real-time data
- Directly interact with devices such as sensors, valves, pumps, motors, and more through human-machine interfaces (HMIs)
- Record process values and events into a historical database
Ignition promotes being different in a few ways, including:
- Modern
- Scalable
- Intuitive
- Powerful
Let’s break those down.
Modern
Ignition is built on Java and uses popular modern languages, like python, for coding instead of custom VBA. In a world where technology is constantly evolving, this sets the software apart in some noticeable ways.
As a relatively new product, Inductive Automation doesn’t need to support 30+ years of installed base. This can be a problem for incumbents in the industry as they can’t abandon their existing customers and need to continue supporting their current software. The cost of re-training engineers, converting old projects and systems, and supporting legacy products prevents many established suppliers from starting new.
Time is also an advantage of Ignition. The installation time, from deciding to download Ignition to having the software installed and ready to develop, is 5 minutes. Compare that with 30 min to 8 hours with other software in our industry. That’s a big deal for system integrators and plant engineers where time is money.
Not only is the SCADA install time short, it also doesn’t require View nodes to have Ignition installed on them. This is because Ignition hosts its HMI screens as a webpage, accessible from anywhere on the network with any browser.
Scalable
Scalability with Ignition focuses on one word that controls engineers aren’t used to hearing: Unlimited.
Ignition licensing has unlimited clients, unlimited tags, unlimited developer seats, unlimited connections to other servers and devices, and unlimited projects. In an industry that often puts arbitrary license limits on everything, Ignition is only limited by the hardware you run it on.
This unlimited scalability mindset is a valuable benefit and helps avoid many issues that controls engineers struggle with now. I know that I have personally had to:
- Combine 3 screens into 1 with layers of visibility on objects to hit a max screen count on our customer’s license.
- Wait 5 weeks to get a single user added to a terminal server license because the customer needed 1 more viewer for their new process line than their license allowed.
- Spend 8 hours troubleshooting communications between a SCADA and a PLC when some new SCADA tags were unable to read data in the PLC. The client happened to run just over their license tag limit and the SCADA software had no indication whatsoever that this limit had been reached.
- Lose 4 hours of driving to a remote facility because the SCADA there didn’t have a “developer” license. Runtime-only licenses are a ridiculous time waster.
Unlimited is an important feature. But there is another, more important advantage when I am developing an Ignition project: It’s intuitive.
Intuitive
Intuitive is a word that’s hard to quantify and thrown around way too much. However, I think the word fits with Ignition.
Inductive Automation has put in the effort to make Ignition easy to use. Everything from Ignition’s modular approach to functionality to the layout of its designer feels far more familiar to the design of other modern software. And if the user doesn’t like the default layout, it is easy to rearrange the designer’s elements on the screen to customize your design experience.
Even the functions that are more difficult to use or locate are made easier with an online manual. Being completely searchable, Ignition’s online manual is both thorough and highly accessible. It is also bolstered by an extensive forum with an active developer and end-user community that are happy to answer questions.
Powerful
Inductive Automation learned from the best of the existing SCADA software in the industry and it shows. Ignition borrows some of the best features from other SCADA software, like:
- Tag browsing of PLCs
- Screen-object template creation
- Tag-group template creation
- Managed and rapid deployment of screen changes
- Advanced alarm management
- Custom reports built in Ignition
You no longer need to manage a development directory for screens or build each set of pump tags individually. These capabilities make Ignition a fast and easy-to-use development environment. When you combine those SCADA advantages with the MES and IIot capabilities of Ignition, you will start to see just how broad the utility of Ignition really is.
Also, Ignition is built on open standards that are easy to support, including:
- SQL
- Python
- OPC UA
- MQTT
All these capabilities combine with Ignitions cross-platform compatibility and view-on-any-device ability to create a versatile SCADA product.
Conclusion
All this is not to say that Ignition is a perfect SCADA. That doesn’t exist. But the combination of modern software, unlimited licensing, intuitive design, and powerful capabilities makes Ignition a good fit for any new build or existing system upgrade.
About the authors
Jason Barry is a Controls Engineer for Hallam-ICS. He has spent his career working on process automation systems in a variety of industries including Chemical, Food and Beverage, Oil and Gas, and Toxic Gas Monitoring. His area of expertise includes Rockwell PLCs, multiple SCADA software, and SQL databases.
Read My Hallam Story
Dalton Sheehan is a Controls Engineer for Hallam-ICS. He is one of the younger hires but has a strong background in the pharmaceuticals industry mainly focusing on compliance integration and OEE studies.
Read My Hallam Story
About Hallam-ICS
Hallam-ICS is an engineering and automation company that designs MEP systems for facilities and plants, engineers control and automation solutions, and ensures safety and regulatory compliance through arc flash studies, commissioning, and validation. Our offices are located in Massachusetts, Connecticut, New York, Vermont and North Carolina and our projects take us world-wide.
You May Also Like
These Related Stories
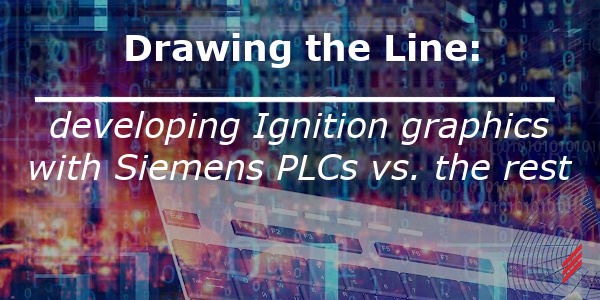
Drawing the Line: Developing Ignition Graphics with Siemens PLCs vs. the Rest
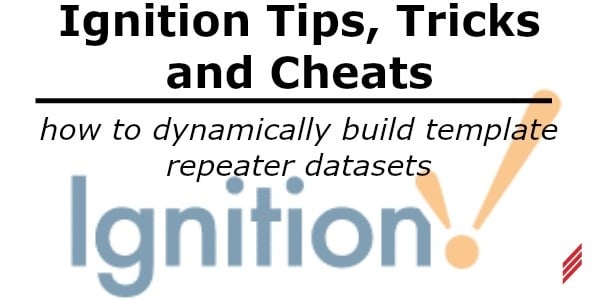
Ignition Tips, Tricks and Cheats-How To Dynamically Build Template Repeater Datasets
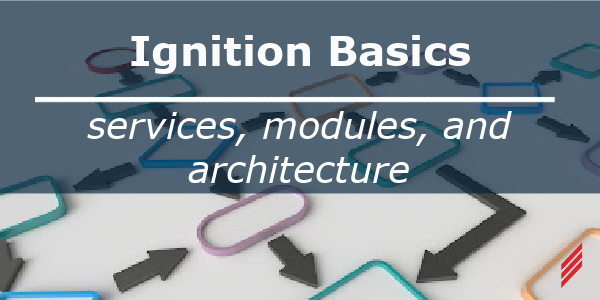
No Comments Yet
Let us know what you think