Why is Infrared Thermography Important for Electrical Equipment?
by Scott King, PMP on Oct 14, 2021 10:28:53 AM
Hallam-ICS provides electrical safety, design, and mitigation services to our clients. We also try to share our knowledge through blogs, white papers, and webinars to help educate electrical and safety professionals. I have written this series of blogs to provide more information about Infrared Thermography. The four blogs in this series are:
- Infrared Thermography for Electrical Equipment
- Why is Infrared Thermography Important for Electrical Equipment?
- Electrical Equipment and Challenges with Infrared Thermography
- The Benefits of Combining Infrared Thermography with an Arc Flash Study
In this second blog, I want to go over the importance of Infrared Thermography and apparent temperature rises in electrical equipment. But first, why is it important? Simply put, to protect your assets by preventing electrical equipment failure but more importantly, to protect your employees from unwarranted fires or heat energy release such as an arc flash event. The number one reason electrical equipment fails is fires involving lighting and power distribution equipment triggered by electrical faults and malfunction. In some cases, death results and in many cases, injury results.
- Approximately 50% of fires are due to unclassified electrical failure or malfunction.
- Approximately 60% of fires are caused by wiring or related equipment.
Another reason it’s important; to meet regulatory requirements OSHA & NFPA:
- 29 CFR 1926.431, Subpart: K = NFPA 70B
- 29 CFR 1926.331-335, Subpart: S – NFPA 70E
Here are some common causes and examples of Electrical Equipment Failure:
- Extreme Load Conditions
- Vibrations and Harmonics
- Mechanical Wear and Stress
- Incorrect Crimping of Connections – could be due to lack of proper cable training
- Poor electrical connections
- Thermal Expansion and Contractions
- Deteriorated conductor insulation
- Bad circuit breaker
Any of these examples could result in extreme temperature differential which can reduce the electrical life of organic insulating materials.
How can you ensure personnel safety and prevent equipment failure?
- Personnel Safety
- Hazard Elimination (NFPA 70E, article 110.1)
- Electrically Safe Work Condition (NFPA 70E, article 110.3)
- Following an Electrical Safety Program (ESP) – (NFPA 70E, article 110.5) & Lockout/Tagout Applied (110.5)
- Electrical Safety Training (NFPA 70E, article 110.6)
- Test Instruments and Equipment (NFPA 70E, article 110.8)
- Equipment Failure can occur when the following does not happen:
- Properly installed and maintained (NEC, NFPA 70E & 70B)
- Conduct Predictive Maintenance measures
Let’s take for example your car. You rely on your vehicle day in and day out to get you to work, to bring the kids to school, get groceries, and drive across the country on a family vacation. When your car breaks down, what does that mean? Did it break down because you didn’t do the proper maintenance on the vehicle? Were the repair costs costly? In most cases, if we didn’t do the proper maintenance on our car there could be a catastrophic failure and it’s likely the repair cost will be excessive and that’s painful. Comes right out of our wallet.
What if you had an accident due to electrical equipment failure and someone got seriously injured or heaven forbid, death results? These are awful thoughts to think about and none of us want that to happen.
It’s the same thing with electrical equipment and components. They are mechanical devices and much like your car, these components need to be maintained or at least monitored. Using IR thermography on a regular cadence as part of your predictive maintenance program will allow you to identify when it’s time to fix or replace a component. In my first blog, I gave an example of a facility manager responsible for daily revenue of $1 million manufacturing high demand devices at his/her plant. They can’t afford or justify electrical equipment failure. It impacts the entire organization, including bottom line and health & safety of employees.
Maintenance and monitoring of electrical equipment is an important part of managing any facility. Infrared Thermography is a proven method to monitor and ensure reliability of the electrical systems to eliminate failure.
I hope this information was helpful and gave you an understanding why Electrical Thermal Imaging is important.
In my next blog, we will discuss Electrical Equipment and Challenges with Infrared Thermography.
About the Author:
Scott King is the VP & National Director of Electrical Safety Services. Scott has been with Hallam-ICS for over 30 years. Scott and his team have been conducting power system studies for over 15 years.
Read My Hallam Story
About Hallam-ICS:
Hallam-ICS is an engineering and automation company that designs MEP systems for facilities and plants, engineers control and automation solutions, and ensures safety and regulatory compliance through arc flash studies, commissioning, and validation. Our offices are located in Massachusetts, Connecticut, New York, Vermont and North Carolina and our projects take us world-wide.
You May Also Like
These Related Stories
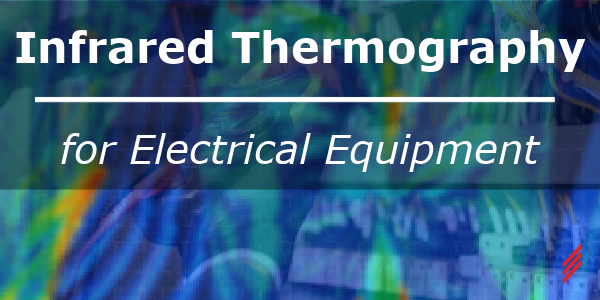
Infrared Thermography for Electrical Equipment
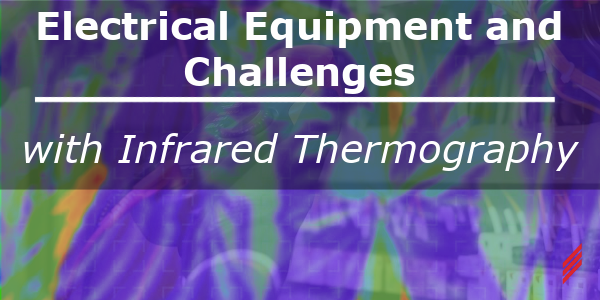
Electrical Equipment and Challenges with Infrared Thermography
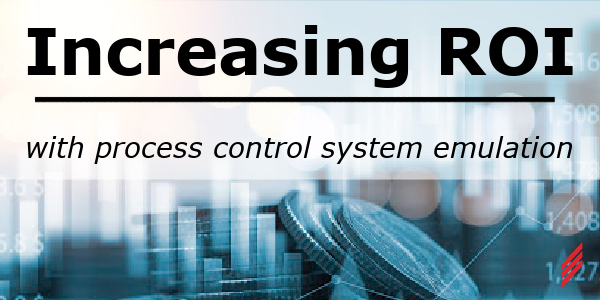
Comments (2)