Infrared Thermography for Electrical Equipment
by Scott King, PMP on Oct 12, 2021 10:30:00 AM
Hallam-ICS provides electrical safety, design, and mitigation services to our clients. We also try to share our knowledge through blogs, white papers, and webinars to help educate electrical and safety professionals. I have written this series of blogs to provide more information about Infrared Thermography. The four blogs in this series are:
- Infrared Thermography for Electrical Equipment
- Why is Infrared Thermography Important for Electrical Equipment?
- Electrical Equipment and Challenges with Infrared Thermography
- The Benefits of Combining Infrared Thermography with an Arc Flash Study
Infrared Thermography for Electrical Equipment
You are the facility manager of a large manufacturing facility responsible for daily revenue throughput of $1 million, on average. Your product is a newly innovated high-tech device in very high demand. It is imperative that all four of your manufacturing lines run flawlessly to meet daily quota. You are entrusted by your superiors because of your experience and track record. Each line depends on sophisticated electrical distribution switchgear for proper optimal performance and operation. An electrical equipment failure could be detrimental to operations. In addition, someone could get hurt!
What can you do to prevent an electrical equipment failure?
One way to safeguard and maintain consistency of your equipment is to provide Infrared (IR) Thermography, which is the science of detecting thermal energy or heat emitted from an object such as a poor electrical connection or a bad circuit breaker. This thermal energy is converted to an apparent temperature and displayed as an infrared image.
In addition to identifying poor connections, IR Thermography is a non-destructive test method that may be used to detect unbalanced loads, deteriorated insulation, or other potential problems in energized electrical components. When we have this information, we can identify electrical equipment that is about to fail or require maintenance and understand the potential onset of a fire or arc flash incident.
Here is how it works. A thermal imaging camera creates a thermogram (image). In the resulting image, the brighter colors (red, orange, and yellow) indicate warmer temperatures by way of more heat and infrared radiation emitted. The purples and dark blue/black indicate cooler temperatures by way of less heat and infrared radiation emitted. Therefore, the bright yellow area indicates the “hot spot” or the location of the electrical fault.
IR Thermography is an example of “Predictive Maintenance” as compared to “Preventative Maintenance”. Predictive maintenance uses data to address an impending failure before it occurs, while preventative maintenance is a scheduled activity, whether actual upkeep is needed or not.
There are several benefits of predictive maintenance, including:
- Visibility on a regular basis of your assets which increases the asset life cycle
- Since this type of maintenance is “as a minimum” typically completed annually, we can predict failures using the ongoing data and trend it
- Increases reliability of the electrical components
- Offers the option to plan necessary downtime (shutdowns) to conduct replacement and/or recommended solutions
- This method is cost effective compared to “Preventative Maintenance”
Preventative Maintenance is:
- Based on periodic inspections and checks
- Asset wear and tear is typically not considered
- You will likely miss detecting a failure prior to it occurring
- Requires trained personnel and the time to continuously check the equipment
- Personnel who understand what to look for
What are the recommended best practices for Electrical Equipment Maintenance?
IR Thermography is a highly effective method for predicting electrical failures before they occur. NFPA recommends infrared inspections be conducted only by trained personnel and on at an annual basis:
- NFPA 70B – Recommended Practices Electrical Equipment Maintenance - industry accepted guideline including OSHA
- “IR inspections should be performed by qualified and trained personnel who have an understanding of infrared technology, electrical component maintenance…”
- “IR inspections require special measures and analysis. Since most equipment is enclosed for safety or reliability can be difficult to scan or to detect radiation within. Therefore, special precautions, including the removal of access panels (equipment covers) might be necessary for satisfactory measurements…”
- Inspection Frequency “routine infrared inspections of energized electrical systems should be performed annually prior to a shut down. More frequent IR inspections (i.e. quarterly or semi-annually) should be performed where warranted by loss experience, installation of new electrical equipment, or changes in environmental, operational or load conditions’”
What makes electrical equipment fail? Temperature Rise of Electrical Components from Heat Energy
- The failure rate of an electrical component doubles for every 10 deg C of temperature rise. A failure rate of 20 deg C temperature rise is typically normal. However, adding 10 deg C to the normal rate of 20 deg C (30 deg C) increases the failure rate by 2X. Add an additional 10 deg C (40 deg C) increases the failure rate by 4X. Regular infrared inspection reduces the likelihood of failure.
I hope this information has been useful and provides you a basic understanding of how IR Thermography works and the benefits of regularly inspecting electrical equipment to alleviate failure.
In my next blog, I will provide examples of what causes these temperature rises and why Infrared Thermography is important.
About the Author:
Scott King is the VP & National Director of Electrical Safety Services. Scott has been with Hallam-ICS for over 30 years. Scott and his team have been conducting power system studies for over 15 years.
Read My Hallam Story
About Hallam-ICS:
Hallam-ICS is an engineering and automation company that designs MEP systems for facilities and plants, engineers control and automation solutions, and ensures safety and regulatory compliance through arc flash studies, commissioning, and validation. Our offices are located in Massachusetts, Connecticut, New York, Vermont and North Carolina and our projects take us world-wide.
You May Also Like
These Related Stories
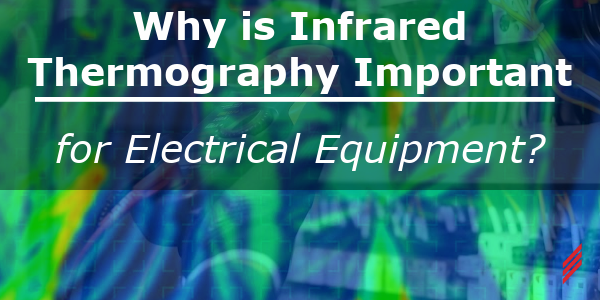
Why is Infrared Thermography Important for Electrical Equipment?
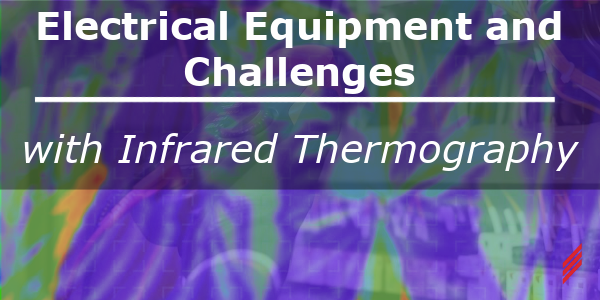
Electrical Equipment and Challenges with Infrared Thermography
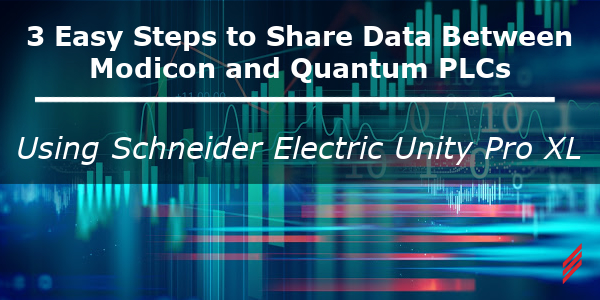
Comments (1)