Don’t Let Overlooked Calibrations Risk the Safety of Your Facility
by Shane Hamlin on Dec 12, 2024 10:30:00 AM
As we conclude this series on Calibration and Metrology, we reflect on why calibrating your equipment is essential. Key reasons included safety, efficiency, quality control, equipment reliability, cost savings, and regulatory. However, you may be asking yourself what exactly needs to be calibrated. While not everything in your facility requires calibration, there are critical items that are often overlooked. Let us look into some of these and discuss how Hallam-ICS can support your business.
We have already covered temperature and weights and measures in previous blogs. These are common calibrations in all industries and are rarely overlooked. If your temperatures are bad, you will consistently see a product that is defective. If your weights and measuring systems are inaccurate, you can see a revenue loss and increased overhead. So, these types of calibrations are generally well-maintained.
Electrical calibrations, pressure calibration, speed and time calibrations, and gas detection calibrations and testing are often neglected. This is because they tend to produce less noticeable issues with your product. However, they are just as important as others previously discussed calibrations. Some of these calibrations are crucial to the product, the equipment, and the environment where your products are created, while others are vital for the safety of your employees.
Electrical calibrations often go unnoticed until they are significantly out of range. These include 4-20mA calibrations for instruments and controls, which ensure accurate milliamperage signals for precise equipment readings. Voltage checks for electronic eyes used in factories production are also crucial, as they are used for maintaining product quality and for ensuring products are consistent at high speeds of production. Additionally, calibrating amperage used by motors can be vital to verify electronic current’s intensity. Excessive wear and tear on a motor can cause breakdowns, which would stop production. Electronic calibrations ensure the accuracy of instruments measuring electrical properties like volage, current, resistance and frequency. These calibrations are essential and should not be overlooked.
Pressure calibrations involve ensuring the devices measuring, you guessed it, pressure, are reading accurately. Incorrect pressure readings can lead to unsafe operating conditions, potentially causing equipment failure, accidents, or hazardous leaks. Pressure gauges, which measure and monitor the pressure of air, gases, and fluids, are critical for maintaining safe pressure levels. If the pressure of certain gases is too high, it can result in catastrophic breakdowns of equipment or even explosions, posing life-threatening risks. Regular calibrations of these devices are essential to the safety of both the machinery and staff. It is commonly neglected until it is too late, but routine maintenance and calibration can ensure the safety of your entire facility. Calibrating pressure transducers is also crucial, as they measure the force being exerted on the surface through pressure readings. While this is less life-threatening, it is important for ensuring product quality and accuracy. Regular calibrations of pressure instruments precise readings, safeguarding your product, equipment, environment, and most importantly, your staff.
Speed, torque, and time calibrations involve verifying the accuracy of equipment speeds and timers. In biotech facilities, centrifuges mix or separate samples, and the speed at which this occurs is important. Any deviation in speed or time can lead to inaccurate separation, affecting the quality of results. Ensuring correct speed and time provides consistent and reliable data outcomes. Motors in industrial facilities require regular calibrations to ensure the speed and torque required to do the job is accurate. This not only prevents product issues but also addresses safety concerns. For example, excessive speed and torque when wrapping metal onto a spool can cause the metal to unwind, posing a safety risk, especially if it occurs around staff. In food service, timers must be calibrated to ensure precise cooking times, such as a 3-minute egg or a 2-hour roast is cooking for the accurate amount of time. Maintaining a regular calibration schedule ensures the accuracy and precision of your equipment, safeguarding both your product and staff.
Gas detection calibration and testing is one of the most overlooked services in all industries. Once the system is installed, people often assume it will continue to function. While this may be true in some cases, it is not always the case, this leads to potential life-threatening issues. Consider your home, you install a carbon monoxide monitor and then never check it again until an incident occurs. The same scenario is true in many industries. Despite being one of the most crucial pieces of equipment, once installed, people just assume it works. This can create dangerous scenarios for the well-being of your facility and more importantly your staff.
You may know that Hallam designs, builds, and installs Toxic Gas Monitoring Systems, but you might not be aware we also test and maintain these systems. While safety is paramount for installing these systems, keeping these systems operational and finely tuned is equally important. Ensuring that gas detectors provide accurate readings of gas concentrations and will detect gas leaks is crucial for the safety of your facility and staff. Although I am concluding this series of calibration blogs, I will be writing one more on challenging, calibrating and maintaining your toxic gas systems.
Each type of calibration is essential for maintaining the accuracy and reliability of instruments across various fields. In biotech facilities, calibration ensures the integrity and reliability of data generated in research and production. In industrial settings, regular calibration of instruments maintains measurement integrity, ensuring safety, compliance, and efficiency. In the food service industry, regular calibration helps maintain food safety standards, ensures food quality, and ensures compliance with regulatory requirements.
Links to Complete Calibration and Metrology blog series:
The Importance of Calibrations and Metrology in Any Industry
Fundamentals of Calibrated Metrology
Why Temperature Calibrations Matter: Ensuring Precision and Safety
I hope this blog series has provided you with a better understanding of the importance and details of calibration and metrology. While there are many more types of calibrations not mentioned here, covering them all would take an entire book. The goal was to highlight some of the often-overlooked calibrations and to encourage you to consider what might need calibration in your facility. I hope this series has helped you better understand your needs. If you have any questions about what your calibration needs might be, feel free to reach out to Hallam. I look forward to having you join me for my upcoming blog on Toxic Gas Monitoring System maintenance.
About the Author
From his diverse work experiences to his current role with Hallam-ICS, Shane has learned the critical importance of not just having the right tools but properly calibrated tools to get a job done right. Having worked across various industries has given him a unique perspective on the importance of precision. In this blog, he will show that no matter what profession you work in, the difference between a job done and a job done well stems from the calibrations of your tools.
Read My Hallam Story
About Hallam-ICS
Hallam-ICS is an engineering and automation company that designs MEP systems for facilities and plants, engineers control and automation solutions, and ensures safety and regulatory compliance through arc flash studies, commissioning, and validation. Our offices are located in Massachusetts, Connecticut, New York, Vermont, North Carolina , and Texas and our projects take us world-wide.
You May Also Like
These Related Stories
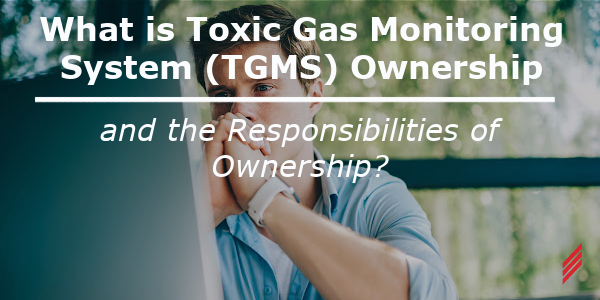
What is Toxic Gas Monitoring System (TGMS) Ownership and the Responsibilities of Ownership?
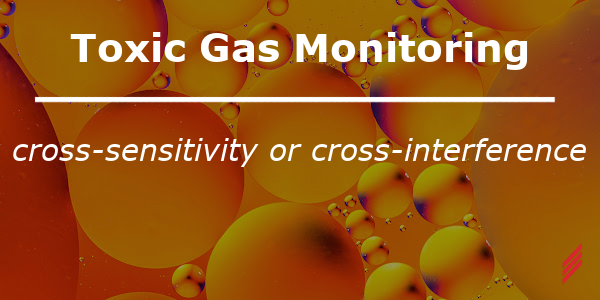
Toxic Gas Monitoring: Cross-Sensitivity or Cross-Interference
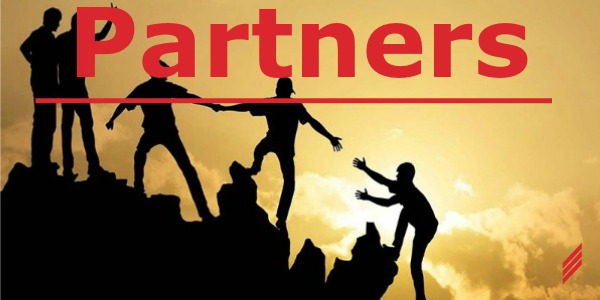
No Comments Yet
Let us know what you think