ARC FLASH & ELECTRICAL SAFETY
MINIMIZE ELECTRICAL HAZARD RISK AND ENSURE WORKERS SAFETY
Single building, campus-wide, nationwide or international, Hallam-ICS can provide arc flash studies, offer mitigation solutions and NFPA 70E training for your facility. We can help you with better electrical system performance as a result of coordination studies for low & medium voltage systems. Your employees will benefit from improved safety with labelling, selecting proper level of PPE and electrical safety training.
ARC FLASH & ELECTRICAL SAFETY SERVICES
Hallam-ICS offers a variety of engineering services to owners, architects, and construction managers who are developing clean, dirty, and dangerous systems. Our comprehensive understanding of high-level business goals and deep technical knowledge will turn your facility into a competitive advantage for your organization.
ARC FLASH ASSESSMENTS
ARC FLASH ASSESSMENTS
INFRARED THERMOGRAPHY
INFRARED THERMOGRAPHY
ELECTRICAL SAFETY PROGRAM COMPLIANCE
ELECTRICAL SAFETY PROGRAM COMPLIANCE
QUALIFIED ELECTRICAL SAFETY TRAINING
QUALIFIED ELECTRICAL SAFETY TRAINING
ARC FLASH ASSESSMENTS
When it comes to electrical safety, the risks associated with complacency are too great to ignore. We perform detailed arc flash assessments and 5-Year Updates to implement and uphold cost-effective solutions for arc flash mitigation.
Our process engineering services include:
- Field Surveys & Data Collection
- One-Line Development & Updates
- Engineered Arc Flash Analysis
- Short Circuit Analysis
- Coordination Studies
- Labeling & Training
- Mitigation Solutions
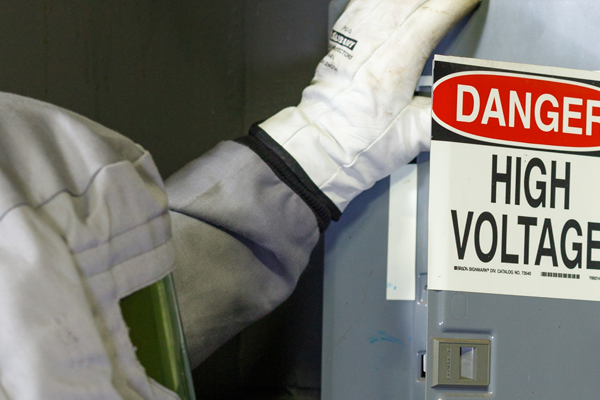
INFRARED THERMOGRAPHY
The number one reason electrical equipment fails is fires involving lighting and power distribution equipment. Using IR thermography on a regular cadence as part of your predictive maintenance program will allow you to identify when it’s time to fix or replace a component.
Our infrared thermography services include:
- IR Thermography
- Systems and Findings Analysis
- Report Generation
- Predictive Maintenance
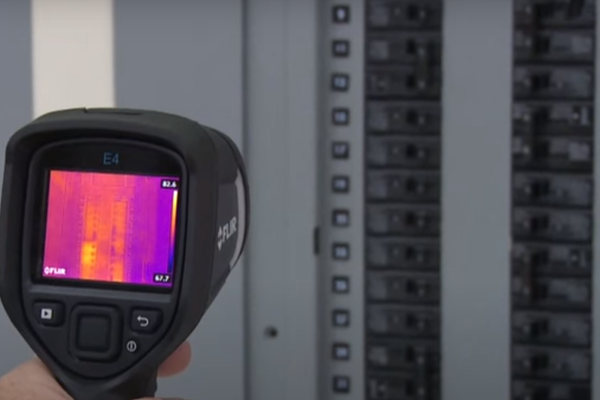
ELECTRICAL SAFETY PROGRAM COMPLIANCE
An electrical safety program ensures employees are trained in safety practices and comply with NFPA 70E, with expert assistance available for compliance. We offer program reviews and new program development.
Our comprehensive program Learning@Hallam is designed to provide organizations with a leading-edge solution for electrical safety training and compliance. With a focus on continuous improvement and tailored solutions, Learning@Hallam offers:
- A wide range of courses
- Skills Evaluation
- Site Safety Audit
- Data Analysis
- Safety Briefings
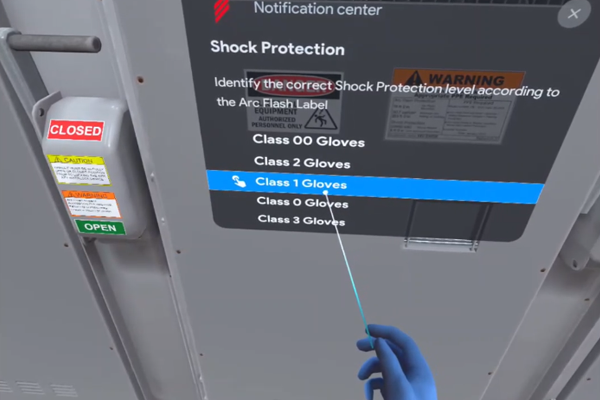
QUALIFIED ELECTRICAL TRAINING
Backed by a team of Electrical Safety Specialists, curriculum developers, and platform managers, our training program offers In-Person, Virtual-Instructor Lead, On-line self paced, and Virtual Reality training, and provides an opportunity for new and tenured employees to meet regulatory requirements and standards. We offer a wide range of training courses, including:
- Electrical Safety Awareness
- Qualified Electrical Worker - Low Voltage
- Qualified Electrical Worker - High Voltage
- Control of Hazardous Energies - Lockout/Tagout
- Human Performance Errors
Our Qualified Electrical Worker Training includes:
- 8-Hr Qualified Electrical Safety Course
- Awareness Training Arc Flash Loss Prevention
- On-Site Training
- 3-Year Retraining Updates
This training is required before an individual can be deemed qualified, i.e. demonstrated skills and knowledge related to the construction and operation of electrical equipment and installations AND has received safety training to identify and avoid the hazards involved.
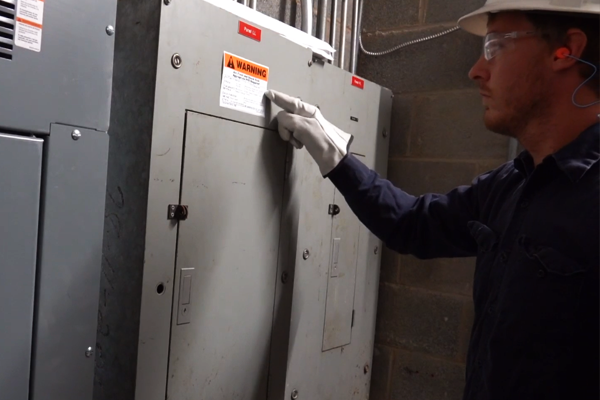
WHY HALLAM-ICS?
Hands-on Knowledge
We are a team of established subject matter experts for conducting arc flash studies and electrical safety training. All work is performed by our degreed electrical engineers who are trained to properly conduct accurate field surveys and utilize infrared thermography.
Helping you reach compliance and safety goals
Improved safety for personnel from labelling, selecting proper level of PPE and electrical safety training so that your employees can work safely and return home to their families after each and every shift.
Solutions for Any Location
In the last 15 years alone, we have completed over 3,000 arc flash studies in the United States, Canada, and Mexico. And whether it is a single building, campus-wide, nationwide or international locations, we can help.
Extend the life of electrical equipment
Better electrical system performance as a result of coordination studies for low & medium voltage systems reduces the risk to employees and your facility.
RELATED RESOURCES
Explore our library of resources to learn more about our exceptional engineering solutions in a variety of applications.
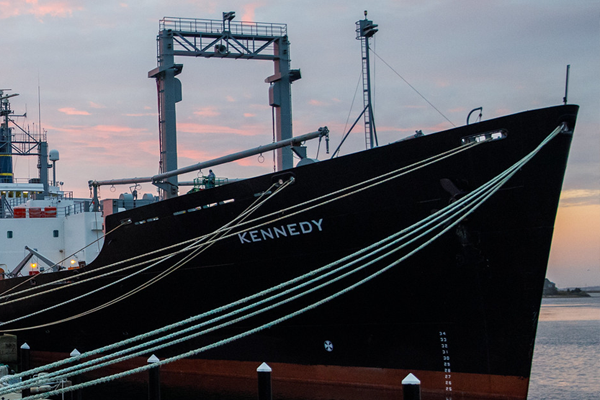
CASE STUDY
Infrared Thermography Inspection
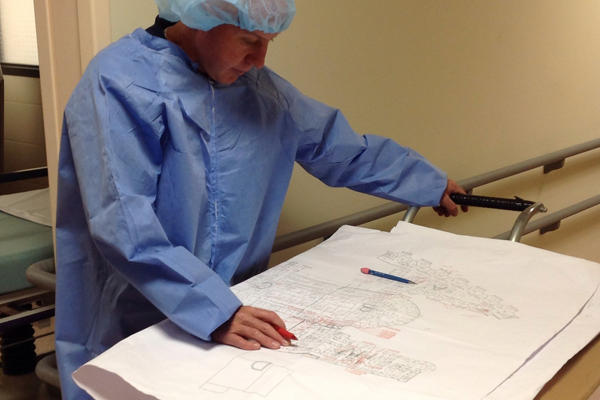
CASE STUDY
Power System Arc Flash
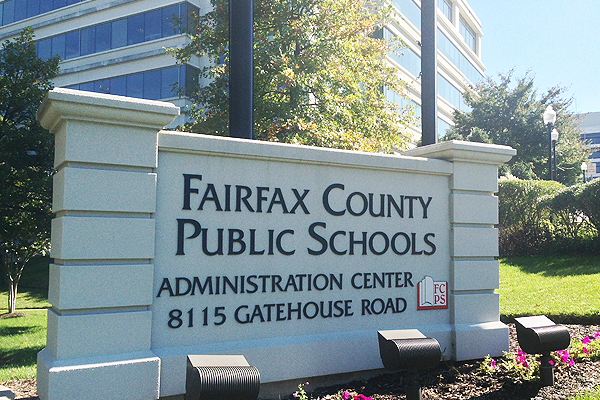
CASE STUDY
Arc Flash Analysis
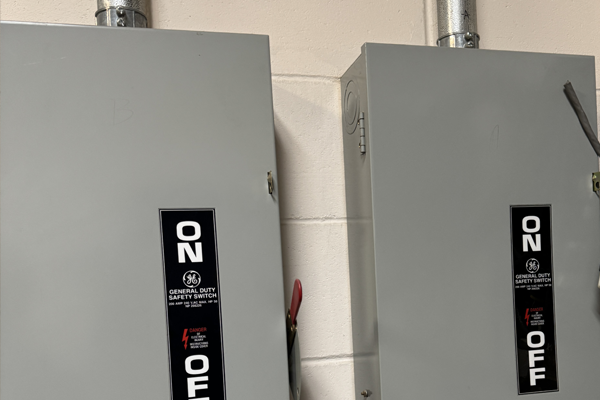
CASE STUDY
Short Circuit Coordination & Arc Flash Analysis
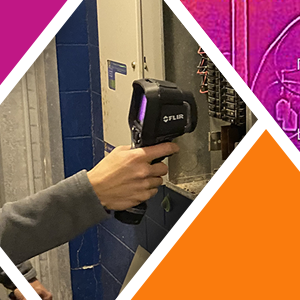
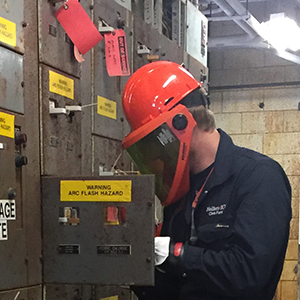
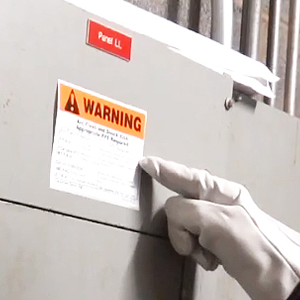
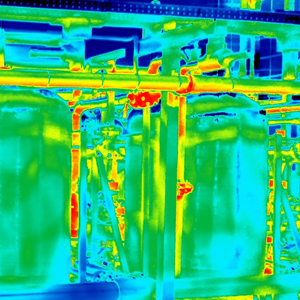
SUCCESS WITH HALLAM-ICS
Clients across industries benefit from our engineering expertise, responsiveness, and project management.
OUR TAILORED APPROACH
Whether you are a semiconductor manufacturer, life sciences company, or industrial plant, our tailored approach ensures that our solutions are perfectly aligned with your unique requirements and timeline. At Hallam-ICS, our approach is rooted in a culture that values collaboration, meticulous attention to detail, and an unwavering commitment to safety. Our team’s engineering expertise and ability to tailor our services to different industries and needs sets us apart, making us a trusted partner in achieving your operational goals.
We follow our proprietary CODES™ process—COMMUNICATIONS, OVERSIGHT, DOCUMENTATION, EXPECTATIONS, and SCHEDULE—to deliver exceptional project quality and consistency. Each project starts with a comprehensive discovery phase, when we gather critical information about your needs and milestones to develop a customized project plan that ensures seamless execution. Throughout the project, we maintain open lines of communication and provide detailed documentation, ensuring that every phase is meticulously managed. Our commitment to technical excellence, combined with our robust customer service, guarantees a successful project outcome and an exceptional customer experience.
FROM OUR BLOG
Stay updated with the latest insights, trends, and expert engineering advice on our blog.
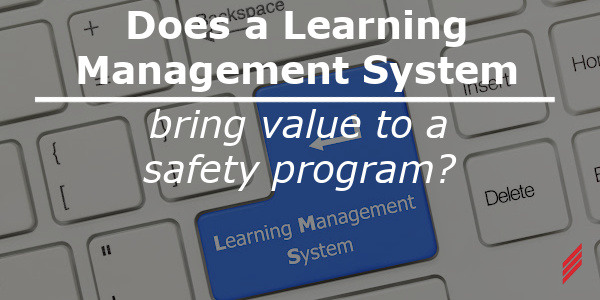
Does a Learning Management System Bring Value to a Safety Program?
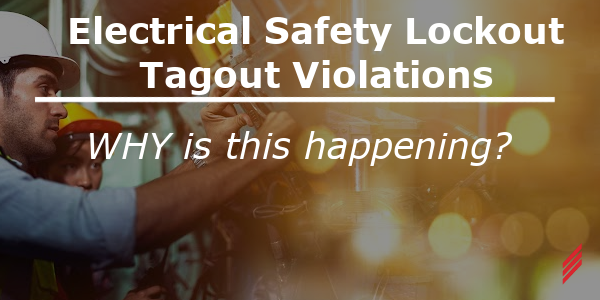
Electrical Safety Lockout Tagout Violations – WHY is this Happening?
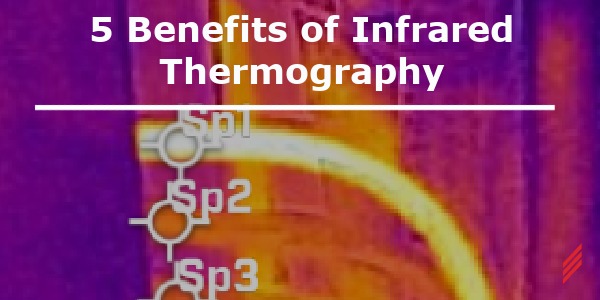