Advancing Automation Technology - Part 1: Server Hardware Requirements
by Jamie Godbout on May 19, 2016 3:05:08 PM
The Advancing Automation Technology series will take an in-depth look into how the latest technology is being used to develop state-of-the-art control systems. We will select various software and hardware packages being used today, and provide you with the best practice techniques on how to apply them, and when you should consider applying each topic.
- Advancing Automation Technology With FactoryTalk® Batch - How is a FactoryTalk® Batch solution different from a traditional PLC project?
- Advancing Automation Technology - Part 1: Server Hardware Requirements
- Advancing Automation Technology - Server Rack Requirements
- Advancing Automation Technology - Layer 3 Core Switch Requirements
- Advancing Automation Technology - How to Specify a Domain Controller
- Advancing Automation Technology - How to Specify a Hypervisor
- Advancing Automation Technology - How to Specify a vCenter Server
- Advancing Automation Technology - How to Specify Shared Storage
- Advancing Automation Technology - How to Specify a KVM Console
- Advancing Automation Technology - How to Specify a UPS
What do you need to build a FactoryTalk Batch Solution?
In my last post, I discussed some of the differences between a traditional PLC project and a FactoryTalk Batch solution. Today, I would like to cover what you will need to implement a FactoryTalk Batch solution that you can use to improve your process control system.
A typical, traditional PLC solution can be seen as a few components put together to accomplish some tasks. The workhorse is the PLC and you have an HMI to provide visibility into that process. However, when implementing a batch solution, you really need to expand your vision and use a systems approach to your process control system. Long gone are the days of islands of automation. In today’s modern process control systems, everything talks to everything and coordination between processes is absolutely critical.
When using a batch solution, each part of the system is modular and must work seamlessly with the other parts of the control system. The same batch control system will run everything from material storage to mixing tanks and reactors along with process heating and cooling equipment.
System Overview
There is too much information to include in a single blog post, so this blog has been divided into three parts:
- Server Hardware Components – will describe the IT equipment needed that will be located within a server room typically enclosed in a server rack.
- Process Control Components – control hardware such as process controllers, I/O, distribution switches, and motor control centers.
- Virtual System Components – virtual servers, operating systems, and require software
Server Hardware Components
Layer 3 Core Switch: A secured manufacturing network will be segmented into several VLANs so a layer 3 switch will be needed. We recommend selecting a layer 3 switch that is managed, has 48 gigabit ports, and is capable of fiber optic up-links with the appropriate SFP.
- Estimated Cost: $800 - $3,000
- Click here for detailed specifications on a layer 3 core switch
48 Port Patch Panel: All Ethernet runs must be terminated at the patch panel. This includes Ethernet cables from the servers inside the server rack. This will help to keep the cabling runs neat and at proper lengths.
Rack Mount LCD Console Tray: The console tray will provide direct video and keyboard access to the equipment in the server rack. This will be needed during the initial setup or when an issue is encountered and remote desktop is not available.
- Estimated Cost: $1,500
- Detail Specifications will be posted soon
Convenience Power Strip: The convenience power strip will provide a place to plug in a laptop or some instrumentation needed to help troubleshoot a piece of equipment in the rack.
Virtual System Platform: A virtual system platform is optional, but highly recommended. It will cut down on the initial start-up costs, as well as the long-term energy and maintenance expenses.
Domain Controller: This is a Windows Server 2012 R2 machine that will authenticate authorized users to the system, and control user permissions on the HMI.
- Estimated cost: $3,000 - $4,500
- Click Here to see my post on ‘How to Specify a Domain Controller’
vCenter Controller: This a Windows Server 2012 R2 machine that will be used to manage the virtual environment and the host servers.
- Estimated cost: $3,000 - $4,500
- Detail Specifications will be posted soon
Virtual Machine Host Server(s): The host server(s) are the powerhouses of the virtual environment. If you try to cut costs on the host machine it will have long term effects on the performance and capacity of your control system. The host machine will be the server that runs all of the virtual servers on your process control system. You also have some configuration options based on your particular requirements.
If you do not require a level of fault tolerance you can get away with a single host machine with integrated hard drives.
- Estimated cost: $10,000 - $16,000
- Detail Specifications will be posted soon
If you do require a level of fault tolerance you will need a second host machine identical to the one specified above.
SAN: A SAN is a separate hard drive array that is accessed via an Ethernet network. You can store your virtual machines on the SAN and most SANs come with built-in disaster recovery and fault tolerance. If you decide to use a SAN you will not require the integrated hard drives on the host servers. You will only need enough integrated storage on the host to hold the ESXi operating system.
- Estimated Cost: $15,000 - $25,000 depending on how much storage you require
- Detail Specifications will be posted soon
Server Rack: The server rack will hold the server and switch hardware as well as manage the Ethernet cables needed to connect the components together. You will require at least a 24U x 19” server rack.
- Estimated Cost: $1,000 - $1,500
- Click Here for detail specifications regarding the server rack
UPS: If your facility does not have a centralized UPS system then you will likely require a UPS in the server rack so that in the event of a power outage your servers will not shut down unexpectedly.
- Estimated Cost: $500-$1,000
- Detail Specifications will be posted soon
KVM Extender Modules: The KVM extender modules will connect the video and keyboard from the LCD console tray to each of the servers in the rack.
- Estimated Cost: $300
- Detail Specifications will be posted soon
Part II of the required system components will address the control layer components that will be distributed out to the manufacturing area. Control components will include process controllers, I/O, motor control, and network requirements.
Click here to see my previous post discussing difference between a FactoryTalk Batch solution and a traditional PLC project.
If you have any questions concerning your process control system or require some assistance, please feel free to reach out to our Controls and Automation experts through our
About the Author:
Jamie has left Hallam-ICS to pursue other endeavors. If you have questions about this article or other Ignition questions, contact Tom Toppin, Process Controls Engineer.
About Hallam-ICS:
Hallam-ICS is an engineering and automation company that designs MEP systems for facilities and plants, engineers control and automation solutions, and ensures safety and regulatory compliance through arc flash studies, commissioning, and validation. Our offices are located in Massachusetts, Connecticut, New York, Vermont and North Carolina and our projects take us world-wide.
You May Also Like
These Related Stories
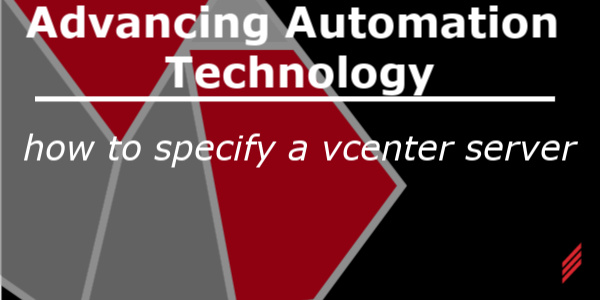
Advancing Automation Technology - How to Specify a vCenter Server
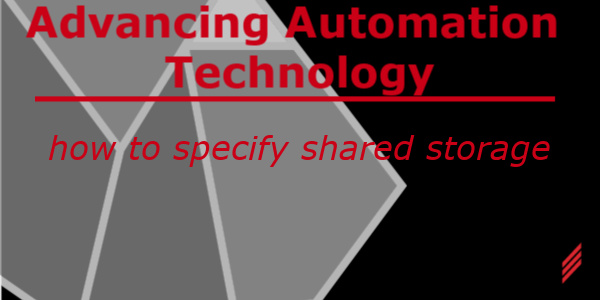
Advancing Automation Technology - How to Specify Shared Storage
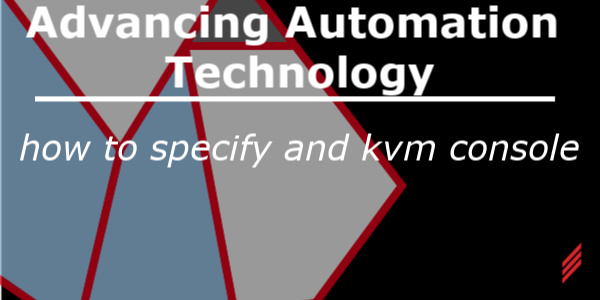
No Comments Yet
Let us know what you think