Advancing Automation Technology - Server Rack Requirements
by Jamie Godbout on May 19, 2016 3:06:32 PM
The Advancing Automation Technology series will take an in-depth look into how the latest technology is being used to develop state-of-the-art control systems. We will select various software and hardware packages being used today, and provide you with the best practice techniques on how to apply them, and when you should consider applying each topic.
- Advancing Automation Technology With FactoryTalk® Batch - How is a FactoryTalk® Batch solution different from a traditional PLC project?
- Advancing Automation Technology - Part 1: Server Hardware Requirements
- Advancing Automation Technology - Server Rack Requirements
- Advancing Automation Technology - Layer 3 Core Switch Requirements
- Advancing Automation Technology - How to Specify a Domain Controller
- Advancing Automation Technology - How to Specify a Hypervisor
- Advancing Automation Technology - How to Specify a vCenter Server
- Advancing Automation Technology - How to Specify Shared Storage
- Advancing Automation Technology - How to Specify a KVM Console
- Advancing Automation Technology - How to Specify a UPS
Server Rack Requirements?
The server rack is the enclosure that will hold the server equipment such as the server computers, network switches, patch panels, power distribution, and cable management equipment. This post will detail the specifications you will need to procure a server rack that will fit your needs for your FactoryTalk Batch process control system.
The primary concern with the server rack is size. It must be large enough to hold all of your equipment. You will be looking for a standard 19-inch rack that is either 24U or 42U tall and 4 feet deep. The 19-inch dimension refers to the space between the mounting rails where the equipment will be mounted. The servers, switch, panels, and shelve will have a standardized width of 19-inches. The dimension xU refers the height of the server. In the world of server racks a U is one slot where a component can be mounted. For example, a 1U server will take up one vertical slot in the rack, where a 2U server will take up two vertical slots. A full height server will generally have 42 to 48U of vertical space where a half rack will have 20 to 24U of vertical space. For the purpose of a control system you will most likely not require more than 24U, but if your rack is going into a server room, as it should, you will most likely want all of your racks to match, in which case, a standard 42U or 48U size rack should be considered. You can use the excess space for other systems or lease that space out to your IT department.
The rack will need to be about 4-feet deep to accommodate the depth of the servers as well as the cable and power management. The smaller the rack, the more difficult it will be to keep the cables running through the rack neat and organized. The last thing you want, is to have a clean server rack with a rat’s nest of cables running through it.
The rack should also include doors on the front, back, and side for maximum accessibility. There will be times when you need to get into a hard to reach spot, and it is wonderful that you can easily pull off the door on the side to get at it.
A full size quality server rack will cost around $1,625.
I recommend APC NetShelter SV PN:AR2580.
Server Rack Power Distribution
Your server and switch equipment is going to require 120VAC power. The power supplied to the rack should be redundant and consolidated. Redundant power means that you will need to run two separate power circuits to the rack, preferably from two separate power panels. This is so that in the event one panel loses power due to a problem or even just regular maintenance, your critical server equipment will not go down. The power needs to be consolidated so don’t try to run several 120VAC circuits to the rack, you will be better off if you run two 220VAC circuits and let the power distribution unit knock that down to 120VAC. This equipment can eat up some power so you want to make sure that you supply enough. A single 20A circuit is probably not going to cut it.
There are power distribution units (PDUs) on the market specifically designed to be mounted in the rear of the server rack. They generally have tabs that fit nicely into slots in the rack that hold the unit in place. I recommend that you look for a unit with a 220VAC plug and will distribute that power to several 120VAC outlets.
It is also helpful to find a switched PDU that offers Ethernet connectivity so that you can monitor power usage or even remotely turn the power on/off for each outlet.
One thing you need to pay attention to are the types of outlet the PDU uses. Server power supplies come with a variety of outlet types as shown on the left. Some have a locking mechanism that will prevent the plug from being pulled out accidently, which is really nice. However, sometimes those mechanisms fail and it can be difficult to pull the plug out when you need to.
I also like to use a combination of the 0U PDU as above and a 1U horizontal PDU. The reason for this is that running all the power lines up and down the server rack can get very messy and I like to keep the rack neat. Also the 0U PDU often doesn’t have enough outlets for everything in the rack, so using a 1U horizontal PDU helps keep the power runs short and provide plenty of outlets. The 1U horizontal PDU gets plugged into an outlet on the vertical PDU and you are in business.
Cable Management
The other major consideration when specifying a server rack, is cable management. It is often overlooked and seen as a way to cut costs, but in truth a messy rack will cost you much more in the long run. You can imagine how embarrassing it would be to accidently pull out a power plug or an Ethernet cable on a critical server because the line was knotted up in a messy installation. Cable management is not very expense nor very difficult. You simply need to make sure that you include some appropriate cable trays, both vertical and horizontal. You also need some place to tie off bundles of cables so that they do not move around.
With Ethernet it is common practice to keep the lines straight, not twisted, and bundled together neatly with zip ties. DO NOT cinch the zip ties too tight or you might damage the geometry in the cable. Cut and terminate the Ethernet runs to appropriate lengths, do not use the loop and tie method to shorten the line, it will just make a mess. Always terminate your Ethernet runs coming into the panel at the patch panel. I also recommend terminating the Ethernet runs from the servers within the rack at the patch panel as well. Avoid using a patch cable to connect the server directly to the switch. It will work, but terminating at the patch panel helps with trouble shooting, and is cleaner. Then you can use pre-fabricated patch cables to connect the ports on the switch to the port on the patch panel. This method also makes it very convenient if you need to reconfigure the ports on the switch. Make sure to label everything on the patch panel so you will know where that line is terminated.
When running power lines try to keep the runs as short as possible and separate from the data lines. The power cables will be much thicker than the data lines so you will not want to run them up and down the whole height of the server rack. This is why I like to use the 1U horizontal PDUs. I can put a couple near the equipment, keeping the power cords short.
In general, I prefer to keep all of my cable management in the back of the server rack. That is where the plugs and the Ethernet ports are located and I generally avoid running cables from the back to the front of the rack. I haven’t found a clean way to accomplish that task yet. This often means that the switch and patch panels are installed in the back of the rack and not the front. So far it has worked out well for me, but this is only a suggestion.
Please keep an eye out for my upcoming posts on how to specify the components needed to build a plant-wide process control system.
Click here to return to Part I of What Do You Need to Implement a FactoryTalk Batch Solution.
Click here to see my previous post discussing difference between a FactoryTalk Batch solution and a traditional PLC project.
If you have any questions concerning your process control system or require some assistance, please feel free to reach out to our Controls and Automation experts through our
About the Author:
Jamie has left Hallam-ICS to pursue other endeavors. If you have questions about this article or other Ignition questions, contact Tom Toppin, Process Controls Engineer.
About Hallam-ICS:
Hallam-ICS is an engineering and automation company that designs MEP systems for facilities and plants, engineers control and automation solutions, and ensures safety and regulatory compliance through arc flash studies, commissioning, and validation. Our offices are located in Massachusetts, Connecticut, New York, Vermont and North Carolina and our projects take us world-wide.
You May Also Like
These Related Stories
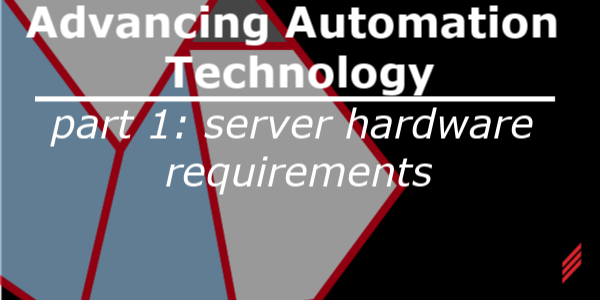
Advancing Automation Technology - Part 1: Server Hardware Requirements
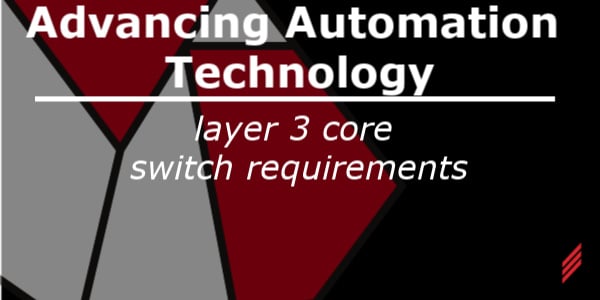
Advancing Automation Technology - Layer 3 Core Switch Requirements
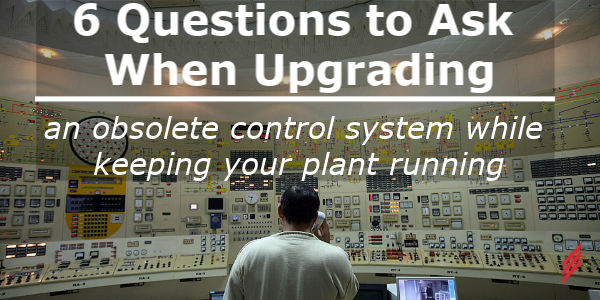
No Comments Yet
Let us know what you think