Advancing Automation Technology With FactoryTalk® Batch
by Jamie Godbout on Nov 21, 2019 12:51:00 AM
Advancing Automation Technology series will take an in-depth look into how the latest technology is being used to develop state-of-the-art control systems. We will select various software and hardware packages being used today, and provide you with the best practice techniques on how to apply them, and when you should consider applying each topic.
- Advancing Automation Technology With FactoryTalk® Batch - How is a FactoryTalk® Batch solution different from a traditional PLC project?
- Advancing Automation Technology - Part 1: Server Hardware Requirements
- Advancing Automation Technology - Server Rack Requirements
- Advancing Automation Technology - Layer 3 Core Switch Requirements
- Advancing Automation Technology - How to Specify a Domain Controller
- Advancing Automation Technology - How to Specify a Hypervisor
- Advancing Automation Technology - How to Specify a vCenter Server
- Advancing Automation Technology - How to Specify Shared Storage
- Advancing Automation Technology - How to Specify a KVM Console
- Advancing Automation Technology - How to Specify a UPS
How is a FactoryTalk® Batch solution different from a traditional PLC project?
Batch processes are somewhat unique in that they often require the use of the same equipment to make many different products. Typically, they involve large tanks, pumps, valves, material feed lines, and some sort of pressure or temperature control. The process would require certain amounts of a specified material to be added to a vessel, and that mixture will often need to undergo some sort of process. By using different materials, adjusting the amounts, or changing the process you can develop a wide range of products.
You could go with a traditional programmable logic controller (PLC) solution and try to build each recipe in the controller; or you could go with a FactoryTalk Batch solution where the recipe is executed on a server and the controller only handles the control of the equipment. The topic of discussion here is what are the practical differences between a traditional PLC project and a FactoryTalk Batch solution.
The primary difference between a traditional PLC project and a FactoryTalk Batch solution is the separation of the recipe execution from the control of the equipment. It is crucial to understand the effect this difference has on your control system. The separation of recipe from equipment means that the logic that controls your recipe is written in terms of process steps, not equipment function.
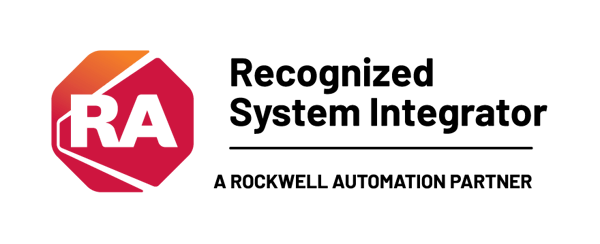
In a traditional PLC project, you would need to build a recipe or a sequence of steps that would open a series of valves, turn on a pump, measure some process variable, and wait until a set of conditions are met before moving onto the next step. This individual creating the recipe will be required to have:
- an intimate knowledge of how the equipment operates
- the knowledge of how the equipment is put together
- a skillset to allow them to create a program in a PLC
- a skillset to design specialized control loops
In a FactoryTalk Batch solution the process automation controller (PAC) only handles the equipment control. If a set of equipment can transfer material from tank A to mixing vessel B the PAC will be programmed to perform that transfer. The sequence of steps to create a recipe is done in the batch server, and is created in the terms of process steps such as:
- heat to 235°C for 30 minutes
- mix for 2 hours
- Add 30 lbs of sugar
- Add 100 gallons of water
The sequence is written using easy to understand block flow diagrams that are intuitive. If you require more than one activity to occur simultaneously the blocks are placed in parallel. If they need to occur in one after another they are placed in series.
This type of architecture promotes modularity in your program code, as well as reusability, and standardization.
In a traditional PLC project if a change is required in the process of a particular product, it can be a great deal of work to reprogram the PLC to accommodate the change. Often times that change will have some effect on another product that uses that same equipment. Using a FactoryTalk Batch solution simplifies process changes to change a block flow diagram or update some parameters to a step. Each product recipe can be independent and can be modified without affecting another product.
When looking at various control system platforms and you have a batch type process, or if you just need to use the same equipment to manufacture many products, then the most efficient, long term and cost effective solution is to go with a FactoryTalk Batch solution over a traditional PLC project. The separation of recipe from equipment along with common PlantPAX library objects, provided for free by Rockwell, significantly drives down development time, and maintenance costs. The end result is a system that is intuitive, where an automation engineer can handle any controller updates, and a process engineer can handle any process changes.
In my next entry we will discuss what is needed to successfully put together a FactoryTalk Batch solution. I will cover everything from server requirements, to software recommendations, to program architecture.
If you have any questions concerning your process control system or require some assistance, please feel free to reach out to our Controls and Automation experts through our
About the Author:
Jamie has left Hallam-ICS to pursue other endeavors. If you have questions about this article or other Ignition questions, contact Tom Toppin, Process Controls Engineer.
About Hallam-ICS:
Hallam-ICS is an engineering and automation company that designs MEP systems for facilities and plants, engineers control and automation solutions, and ensures safety and regulatory compliance through arc flash studies, commissioning, and validation. Our offices are located in Massachusetts, Connecticut, New York, Vermont and North Carolina and our projects take us world-wide.
You May Also Like
These Related Stories
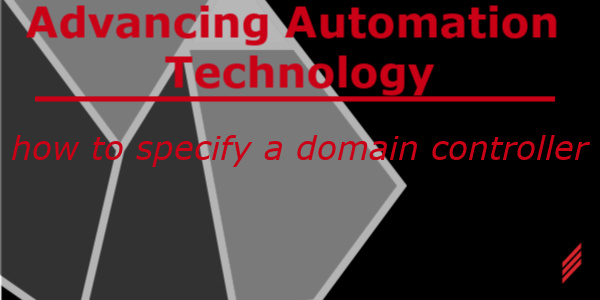
Advancing Automation Technology - How to Specify a Domain Controller
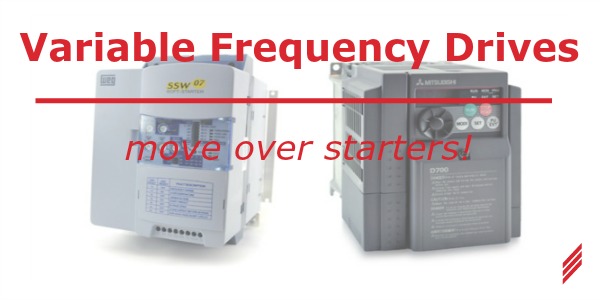
Variable Frequency Drives: Move Over Starters!
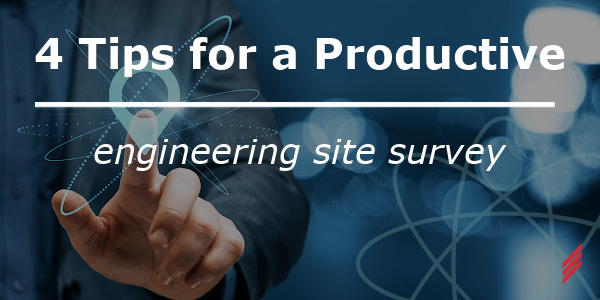
No Comments Yet
Let us know what you think